Curing is a can of worms. When the concrete is at its design strength, it can be in service. When concrete testing (to test design strength) is done they put the cylinders in a sheltered place to prevent the sun from heating the concrete up. They cover the tops and then put a foil insulation over the top. The next morning they pick the cylinders up and put them into optimal curing conditions. Minimal water is lost from the test concrete. And then test the cylinders at the 28 days. The 28 days is just a yardstick. It is a uniform benchmark. You can buy an E (early) mix being E3 or E7 vs an N mix,meaning that an E3 32:20:80 mix has to attain 32MPA in 3 days instead of the required 32MPA in 28 days as required in a normal N32:20:80 mix.
In practice, the concrete is normally poured outdoors. The surface is open and water comes to the surface and evaporates off. The amount of water being lost from the concrete affects the strength, (as does the amount of water in the concrete). This is only an issue above 30 degrees C according to a report from the CSIRO going back 45 years. (I will not be producing that report) Above 35 degrees hot weather must be considered when pouring. As soon as practicable, steps must be taken to ensure minimal water loss from the concrete, keeping as much water in the concrete for hydration purposes.
The majority of my work was tiltup panels. The strength required varied from engineer to engineer for similar purposes. In the main we were required to use N32MPA and lift at a minimum of 25MPA. In Perth and a lot of other places if the overnight temperature is above 15 degrees, 25MPA is obtainable overnight. even on a very cold night, you still get 17MPA. When we have to lift the next day, we cover the finished panel with black plastic while there is still sunshine and then insulation overnight. Guaranteed 25MPA plus the next morning (we put a test cylinder in the same environment).
We started making panels with 20MPA (note the pullout strength for a lifter is only 3.5MPA and a 5:1 safety factor makes it 17.5MPA) and lifting at 21 days. This then went to 25MPA and the norm is now 32MPA and lift nominally 7 days. The engineers are specifying 40 and 50MPA for similar panels with no justification and little consideration that at higher strength there is less flexibility and cracking is more prone.
So, I do not think that reduced curing time is a gamechanger and an unique selling point. The thinking of the engineering fraternity has to change for that. It will be up to the individual to design a mix that will get the desired strength in the designed timeframe. And they will be able to do so with the use of edencrete.
The more I look at this the stronger my belief that edencrete works because it entraps the free water in the concrete and makes available for the hydration process throughout the concrete, meaning that the water is available in everyplace it is required. Entrapping the water means minimal pores meaning less weak spots, and with water available throughout the concrete means that full hydration occurs without patchy areas where too much free water has dissipated. (i also believe that there is a catalytic reaction) This I think is the true unique selling point.
- Forums
- ASX - By Stock
- EDE
- Similar materials
EDE
eden innovations ltd
Add to My Watchlist
0.00%
!
0.2¢
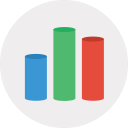
Similar materials, page-48
Featured News
Add to My Watchlist
What is My Watchlist?
A personalised tool to help users track selected stocks. Delivering real-time notifications on price updates, announcements, and performance stats on each to help make informed investment decisions.
|
|||||
Last
0.2¢ |
Change
0.000(0.00%) |
Mkt cap ! $8.219M |
Open | High | Low | Value | Volume |
0.2¢ | 0.2¢ | 0.2¢ | $831 | 418.4K |
Buyers (Bids)
No. | Vol. | Price($) |
---|---|---|
84 | 206703019 | 0.1¢ |
Sellers (Offers)
Price($) | Vol. | No. |
---|---|---|
0.2¢ | 13750636 | 7 |
View Market Depth
No. | Vol. | Price($) |
---|---|---|
1 | 25000 | 0.002 |
84 | 206703019 | 0.001 |
0 | 0 | 0.000 |
0 | 0 | 0.000 |
0 | 0 | 0.000 |
Price($) | Vol. | No. |
---|---|---|
0.002 | 13750636 | 7 |
0.003 | 38183101 | 35 |
0.004 | 13369543 | 14 |
0.005 | 3075777 | 7 |
0.006 | 943493 | 3 |
Last trade - 15.27pm 15/07/2025 (20 minute delay) ? |
Featured News
EDE (ASX) Chart |
The Watchlist
HAR
HARANGA RESOURCES LIMITED.
Peter Batten, MD
Peter Batten
MD
Previous Video
Next Video
SPONSORED BY The Market Online