As the hunt for more efficient batteries continues, Queensland energy tech company AnteoTech has sharpened its focus on the development of its silicon anode binder technology and pure silicon anode design that it claims can deliver an up to 35% improvement in energy capacity when compared to current high energy battery cells.
JUNE 12, 2023
DAVID CARROLLGraphite has served as the dominant anode material for much of the early phase of lithium-ion battery chemistry but Brisbane-based AnteoTech is now seeking to commercialise its silicon anode technology which it says delivers a performance-enhancement trifecta – increasing battery capacity, decreasing charging times, and lowering costs.
AnteoTech Head of Clean Energy Technologies Business Manuel Wieser said the company’s proprietary AnteoX additive reinforces battery binders and helps maximise the performance of silicon-containing anodes through increasing the energy density, cycle life, and cost efficiency of batteries for electric vehicles (EVs), energy storage systems, and consumer electronics.
“The industry has experienced incremental improvements in energy density but … improvements that can be attained by the use of conventional anode and cathode materials are approaching their limit,” he said. “Which is why we are seeinga spectrum of material and cell chemistry innovationsthat are pursued by the major cell manufacturers and automotive OEMs (original equipment manufacturers).”
Weiser said after pure lithium, elemental silicon has the highest theoretical energy storage capacity for lithium ions. In comparison to graphite, silicon can store up to 10 times more lithium ions by weight and up to three times more by volume.
“This means that the more silicon is incorporated into the anode the smaller and lighter the anode and consequently the full battery becomes,” he said. “This translates into battery cells that can store the same amount of energy in a smaller volume or more energy in the same volume.”
“Ultimately, this translates into electric vehicles with additional driving range without having to change the dimensions of the battery pack or in wearable devices or consumer electronics that last longer between charges.”
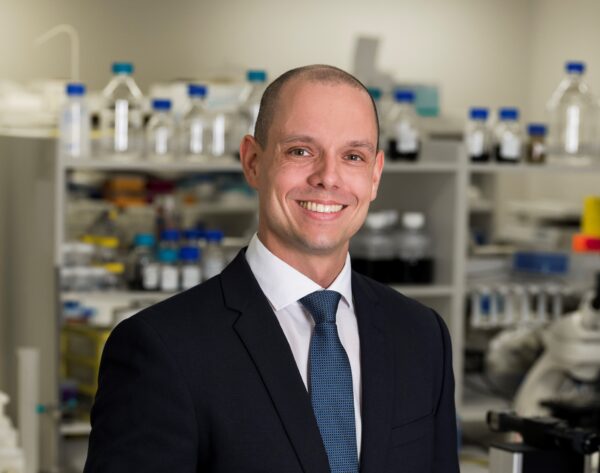
Manuel Wieser, head of AnteoTech’s clean energy technologies business.
Image: AnteoTech
Weiser, who is scheduled to give a talk on the future direction of lithium-ion battery chemistry at theEnergy Nextconference to be held in Sydney on 18-19 July, said the shift to silicon also offers benefits when it comes to charging times.
“Given that the electrode reduces in thickness with an increase in silicon content, silicon anodes can also enable fast-charging performance for electric vehicle applications due to the shorter lengths ions and electrons have to travel through the electrode thickness,” he said.
Weiser said the anode electrode thickness of pure silicon anode designs can easily reduce up to three times compared to conventional graphite-based anodes.
Silicon does however have drawbacks, including that it expands by up to 280%, given its ability to store more ions compared to conventional graphite materials, and Wesier said if not addressed appropriately this leads to rapid capacity fade and battery life degradation.
The highcost of siliconis also an issue but Wieser said the key differentiator of AnteoTech’s silicon anode approach is that it uses industrial silicon which is more than eight times cheaper on a dollar per kWh basis compared to other silicon materials in the market.
“AnteoTech’s silicon anodes contain up to 90% of silicon, where mass-produced cells currently contain silicon at levels that are lower than 10%,” he said. “In essence, the company provides the smarts to make this crude silicon work extraordinarily well by pairing the anode design with proprietary technologies.”
Weiser said AnteoTech has already demonstrated pure silicon anode battery cells that achieve 500 full charge and discharge cycles while retaining 90% of the battery’s initial capacity with the full silicon anode product being in late-stage development.
AnteoTech is currently looking to scale up production of AnteoX with a first manufacturing facility being established in Brisbane which will be able it to produce 20,000 litres in its first full year of operation.
The move comes after AnteoTech earlier this year signed separate non-binding agreements with Swiss-based battery developer Wyon AG and Trinseo Europe, a division of global plastics manufacturing conglomerate Trinseo.
The partnership with Trinseo aims to improve the binding processes in silicon anode battery construction, while the partnership with Wyon seeks to develop and test AnteoTech’s anode design to deliver a material improvement in the performance of Wyon’s battery cells.