@addinvest, I am not an electronic engineer nor work in the AM sector so i can't respond to your technical questions. However, I have read enough articles, talked to a number of AM industry participants and have formed an view based on my research. I invest in a number of disruptive technologies and you will see this from my posts on HC. As a result I have invested according to my understanding as well as the my own risk vs reward proposition of A3D.
Yes, speeds of competitor printers have increased over time but there hasn't been a step change in the AM industry and I believe it sometimes takes a flash of brilliance or going back to first principles to remove rate limiting factors. I believe MCP is once such rate limiting factor. Are we there yet, no...there are challenges to overcome but are we heading the right way, IMHO yes!
One of the articles critiquing MCP tech was done by Fabbaloo. Kerry seems to think the MCP tech valid and responsible for the print speeds!
https://www.fabbaloo.com/blog/2018/11/15/aurora-labs-reveals-secret-to-3d-printing-1000kg-per-dayAurora Labs Reveals Secret To 3D Printing 1000Kg Per Day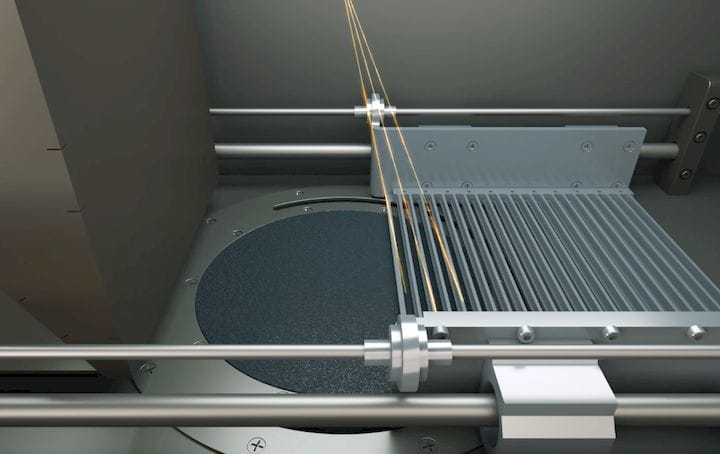
The mysterious multi-layer metal 3D printing process is revealed [Source: Aurora Labs]
Aurora Labs finally leaked the secret to their concept for 3D printing 1000kg of metal per day.
The Australian company has envisioned a powerful, high volume, metal 3D printer that can be used to quickly produce large metal spare parts in remote locations. This concept could be extremely popular, as it would potentially save enormous downtimes for oil & gas, mining and shipping industries who would otherwise lose copious amounts of operational time while awaiting lengthy shipments of spare parts from distant warehouses.
But to achieve this lofty goal the company believes it requires a metal 3D printer to be able to produce objects weighing 1000kg in a single day. This print volume goal has never been achieved or even approached by any known vendor.
To date Aurora Labs has produced an interesting
experimental 3D metal printer that can actually mix powders on the fly to create dynamic alloys, but we were told that machine uses an entirely different process that was not able to scale up to the 1000kg goal. Instead, they said, an entirely new metal 3D printing process was being developed.
Aside from the knowledge that the mystery process used the familiar – and slow – powder bed fusion process, wherein a powerful laser sweeps across a bed of flat metal powder, we knew nothing more.
It was a curious proposition to us, as the powder bed fusion process is well known to be extremely slow. Each layer is scanned by the laser, and then a recoating process lays down another fine layer of powder. During the recoating process, the lasers are idle because they must print only on flat surfaces to ensure the laser target remains in focus.
So how could Aurora Labs possibly use this tedious process to produce 1000kg objects in a single day?We just found out how.
Their method employs two key features.
First, they have managed to produce a recoating tool that can quickly lay down a layer of powder, but that also includes the ability to immediately lase the freshly lain powder – BEFORE THE RECOAT IS
COMPLETE.
Secondly, they do this MULTIPLE TIMES during a single pass.
This is a bit hard to visualize, but essentially they drop and flatten a layer, and immediately follow its deposition with any laser energy required on that layer. But shortly afterwards the second layer is also lain down, also being lased immediately. And a third, fourth and so on.
This is done through an ingenious mechanism that looks like a vane, shown at top. This circular plate slides across the build volume to deposit multiple layers in one pass. In the period gaps between each deposition, the lasers are used to apply energy to the exposed layer.
Observe these screenshots of the process:
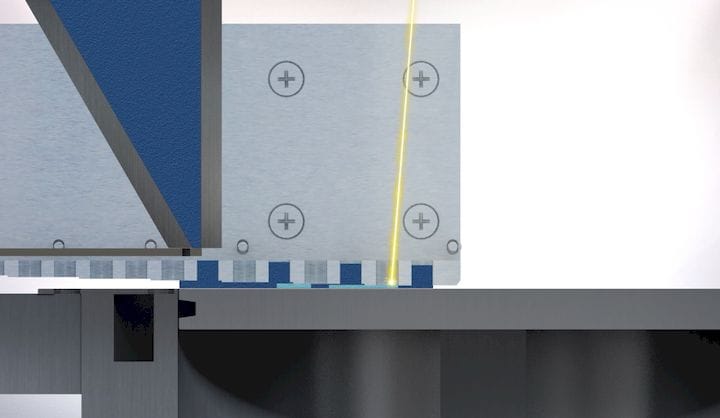
A recoating plate slides over the print bed, gradually depositing layers and allowing space for laser beams to energize the surface [Source: Aurora Labs]
Here we see the layer deposition beginning, and one laser beam is visible deploying energy to the exposed surface through a gap. But also note that the next layer is immediately being deposited on the left.
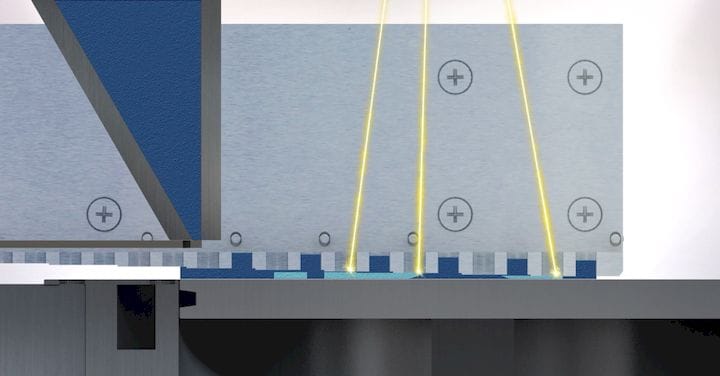
Multiple laser hits pass through gaps that expose each cascading layer of metal powder [Source: Aurora Labs]
As the plate proceeds across this enables multiple layers to be deposited and energized in a single pass. You may see, as in this diagram, different layers being energized at the same time.
This process could potentially be sped up by employing multiple lasers.This is quite revolutionary. It allows many layers to be deposited very quickly. In the top image I count 23 deposition mechanisms, meaning this configuration could deposit 23 layers in the time it would normally take to execute one layer. That is a very dramatic difference in print speed.Obviously there will be an incredible amount of tuning required to ensure the machine is able to successfully 3D print an object using this process. One aspect I’m wondering about is how they manage to keep the laser in focus as the distance between it and the top of the powder seems to change as the plate moves. Perhaps they gradually tilt the build surface?
That’s only one question of many that might be asked of this very unusual process. But on first look it seems that it could work and indeed be scaled up: simply add more layers per pass. Add more energy to fuse particles faster and thus move the plate faster. Make the plate wider to lase more material per pass. This is a totally scalable concept.Aurora Labs has previously said they’ve managed to
test simplified versions of this concept successfully so it would seem they know this approach will work. Now they must proceed with their development and hopefully achieve the incredible ability to 3D print 1000kg of metal in a single day.