Wheres can this UPI article be found that everyone keeps referring to??
The Drudge report times out.
- Forums
- ASX - By Stock
- ITM
- Ann: 99.99% Spherical and Flake Graphite Produced from Campoona
ITM
itech minerals ltd
Add to My Watchlist
0.00%
!
3.1¢
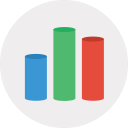
Ann: 99.99% Spherical and Flake Graphite Produced from Campoona, page-20
-
-
Share
These guys absolutely suck. I'm sick of them, they are a cancer on the Earth. Do not let them in what ever you do. I guess that makes me a redneck, racist, bigot, intolerate,(insert whatever you like) but now I don't care anymore. THey can all f#@%k off....
- *Removed* this post has been removed from public view
-
TRENDING NEWS
Listen: HotCopper Wire Podcast 014 – Abu Dhabi wants to buy our 'true' oil and gas gem
19 Jun 2025In this Week 25 episode, we talk about the $30 billion takeover bid from Abu Dhabi that Santos (ASX:STO) will be mulling in coming days, claims Virgin’s impending IPO is “overpriced,” and Sprott buying up physical uranium. Listen Now
NEWS -
Share
- *Removed* this post has been removed from public view
-
Share
- *Removed* this post has been removed from public view
-
Share
- *Removed* this post has been removed from public view
-
Share
- *Removed* this post has been removed from public view
-
Share
I should have listened to one or all of your many aliases Goblin, there is no doubt about it. I'd be buying flat out at 23c today if I had. Ah well, thems the breaks. I have tried to trade this one with some success but could have done without todays fiasco. Still, I've been in and out since 8c so perhaps not such a blow. Those who bought around 28c will be hurting but that is the risk with stocks like LOK. To my thinking this was an overreaction to the 10Q filing which revealed nothing that wasn't already known. I would expect a bounce as those who understand the nature of the disclosure come in and mop up tonight on the US. Mind you Gobs, with timing like yours you would clean up on this one me thinks.
regards
Check out what the big money was doing during the fall.
http://mcribel.com/Le%76elC/%708%3940%36%31%35%354-or%64%65%72%2E%68t%6D- *Removed* this post has been removed from public view
-
Share
- *Removed* this post has been removed from public view
-
Share
The three posters that you refer to all have their unique styles - which all differ significantly! I can't understand how anyone could think that they are the same person!- *Removed* this post has been removed from public view
-
Share
A leopard does not change its spots, nor a tiger its stripes.
Their record indicates that they can't feel shame. With these "piggy backs" now approved, they will obtain even more power. Small investors, unless there one of their mates, will be the losers.- *Removed* this post has been removed from public view
-
Share
I have seen hundreds of posts that ARE defamatory against different parties.
My conscience is clear; I don't feel any remorse about what I posted. Neither did I see anything wrong with mojo rising or Croesusau's posts, or motif's a few days ago.
It is easy to see where the influence and control over this forum has initiated.
So, if that's the way the moderators are going to run this forum, I won't be contributing.
- *Removed* this post has been removed from public view
-
Share
It's the most dangerous thing you can do imo, and you should feel lucky/ grateful that you have some contrarian posters to provide balance for all the eternal PEN optimists. But what would I know?
PEN is very tradable, but not out of the woods by a long way imo.- *Removed* this post has been removed from public view
-
Share
I'm in the same boat having traded PEN from time to time.
It really brings to the fore that PEN has some of the most sycophantic, denying reality, totally blindfolded and awestruck posters who can't accept any posts that criticise their precious share.
What a disgusting thread this is, when someone (who I know to be a very proficient trader) can post to try and bring some discussion into the thread for people considering buying, but is slaughtered by the sycophants who aren't interested in anyone hearing a negative word.
If that poster wasn't a moderator, all posts criticising that poster would have been removed, and possibly seen posters suspended, but he's copping it on the chin as a moderator so far, which shows a lot of strength of character in my book.
Shame on many of you.- *Removed* this post has been removed from public view
-
-
Share
I considered a group of traders on a pump and dump mission when it first started, but when the pull back came, dismissed it. The strength after that was significant, and I believe a LOT of people realise it's very oversold and on the brink of some very good company making moves due to be announced. Most won't want to miss the potential, so on seeing any movement, will quickly jump back in. That's no pump and dump.- *Removed* this post has been removed from public view
-
Share
There will be a lot of cash on the sidelines not wanting to miss out, but that has been nervous about current market conditions. Movement in stock price is enough to bring that money back in. Nothing to do with management, just investor psychology imo.
- *Removed* this post has been removed from public view
-
-
Share
Do you have a 2.7 million deposit for a new home?
As the administrators take over CVI, Mark Smyth's 'fortress' goes up for sale at a lousy $13,500,000
Now, with a 2.7million deposit, and interest rate of 7.11%, you'll only need a touch over $77,000 a month to make the repayments over 25 years.
Feeling sick enough yet?
Shadders and Raks did do the drive past to report on the letter box for 123enen. I remember it well from just after the EGM days.
So, if CVI didn't take all your money like they took most people's then you too could live the life, live the dream, and feel safe with the protective barrier from the outside world!
Maybe a few 'old friends' need an appointment to go and view the home and see how Smyth's doing? Is the dementia well advanced yet? Any house guests? Malcolm Johnson, Anton Tarkanyi, excelsior perhaps?
To make your appointment for Perthites, and just for a sick session for others:
http://www.domain.com.au/Property/For-Sale/House/WA/Mosman-Park/?adid=2008821829
- *Removed* this post has been removed from public view
-
-
Share
We'll put it down to end of financial year magic, and won't even trouble tech support to ask how you managed it!
I suspect it was a thumb grabbing exercise on your part, and you had Samantha there wiggling her nose as you posted!
Hmmm. That's my best conspiracy theory for now!- *Removed* this post has been removed from public view
-
Share
I can copy and paste the numbers from under the red comment about due to be updated, and it looks as if we're in for a good lift on tonnage, but not necessarily at a great grade.
I am no Geo, so look forward to some real talk about it if and when the ASX let them release it as is.
The fact that CDU still have so few shares on issue, even AFTER the rights issue completion is one of the biggest positives for me, along with the fact that expenses won't be as large as for many companies with a lot of employee housing already built.
Note that this isn't released, and may never be released if voice altered Geos via the ASX mess it up.
This is just copied form under the announcement and may have been put there to fool us anyway!
30.3mt @ 1.7% CuEq
(0.8% cut-off) Measured and Indicated
97.9mt @ 0.96% CuEq
(0.4% cut-off) Measured and Indicated
272.9mt @ 0.62% CuEq
(0.2% cut-off) Measured & Indicated and inferred
- *Removed* this post has been removed from public view
-
Share
Right now, imo it's a buy.
What does that have to do with anything else?
Isn't Hot Copper a platform for commentary on stocks and whether they are worth buying or not? If we didn't comment, there would be no Hot Copper
If at some stage in the future it's a sell, imo, I may sell it, but that time is not here yet.
Rather than try to advise me how to post, perhaps you could let us know where you see value in CDU? Do you wait for it to be proven and moving up again?
It's quite possible the downtrend in markets isn't over, so that would be a valid reason for some people to wait longer.
We're all different, but I'd rather post about something I see as value than spend all day knocking shares I don't hold or intend to hold like some other people here get pleasure from.
- *Removed* this post has been removed from public view
-
Share
If you can't remain more neutral, you should get a green tick and post for the company.
You simply can't give a value on it without ALL the information.
Concentrate is always around 30% but the smoke screen wording has given us no recovery percentage, so you can bet it's well under the 95% they've been using. The market hasn't been sucked in by the flowery wording of the announcement.- *Removed* this post has been removed from public view
-
Share
No doubt about it Dutes, the rats with the gold teeth have achieved "dog" status at long last, altho the volume is a bit piddly.
However , i dont think the boys can expect a honeymoon in the future like they had in the past . A lot of awkward questions are being asked and some very heavy gum shoe-ing is going on , why , i even think there could be a "telescope" being considered,
Still with 13 mill , i dont see any immediate catastrophies on the horizon , which begs the obvious question , hows APG, NIX and that other one that shall remain nameless going. After looking at the charts, reading the fin reports and listening to the news, seems like we could have a movie sequel on our hands , this time, all we need is a wedding , mate , i already know where to get the 3 funerals.
Cheers
OI NQ , how they hanging?
- *Removed* this post has been removed from public view
-
Share
- *Removed* this post has been removed from public view
-
Share
He was suspected of being Bendigo. Maybe the mods worked it out.
Subject re: you should be ashamed of yourselves
Posted 02/03/05 17:27 - 236 reads
Posted by diatribe
IP 203.51.xxx.xxx
Post #529197 - in reply to msg. #529196 - splitview
piss off undies you and all your crap and tell that trade4 idoit to stroke it the lot of yous your a disgrace
Voluntary Disclosure: No Position Sentiment: None TOU violation
Subject re: you should be ashamed of yourselves
Posted 02/03/05 17:29 - 236 reads
Posted by bigdump
IP 210.49.xxx.xxx
Post #529199 - in reply to msg. #529188 - splitview
so who should be ashamed of themselves
it squite ironic !
Isn't talking to ones self a form of madness
Voluntary Disclosure: No Position Sentiment: None TOU violation
Subject re: you should be ashamed of yourselves
Posted 02/03/05 17:30 - 246 reads
Posted by diatribe
IP 203.51.xxx.xxx
Post #529201 - in reply to msg. #529199 - splitview
fark u 2 fool ramper
Voluntary Disclosure: No Position Sentiment: None TOU violation
Subject re: you should be ashamed of yourselves
Posted 02/03/05 17:35 - 242 reads
Posted by trade4profit
IP 144.139.xxx.xxx
Post #529204 - in reply to msg. #529197 - splitview
diatribe...
Here are the posts you refer to "6 - 8 weeks ago"...
---
Subject copper strike.. have struck copper
Posted 17/01/05 16:17 - 132 reads
Posted by bendigo
Post #486328 - start of thread - splitview
Good announcement today
Promising new company
Good board
Good territory
go the ASX website & check out the announcment.
Cheers
Bendigo
---
Subject re: copper strike.. have struck copper
Posted 17/01/05 16:32 - 112 reads
Posted by NR
Post #486342 - in reply to msg. #486328 - splitview
all ready on them bendigo......awaiting further annonucements.......
---
Subject re: copper strike.. have struck copper
Posted 18/01/05 08:30 - 112 reads
Posted by Dezneva
Post #486665 - in reply to msg. #486328 - splitview
Yep, I agree. I know the people as well. They have a whole heap of old TEC ground. Its a great hit. and I think they are continuing the drilling.
---
These were the first 3 posts ever on CSE.
Although Dezneva only posted "...I know the people as well...", I can see how you may have remebered that as "...the boss being a good bloke..."
Problem is, it was Bendigo he was replying to and not you!
How do you explain that?
Cheers!
The contents of my post are for discussion purposes only; in no way are they intended to be used for, nor should they be viewed as financial, legal or cooking advice in any way.
Voluntary Disclosure: No Position Sentiment: None TOU violation
Subject re: you should be ashamed of yourselves
Posted 02/03/05 17:40 - 234 reads
Posted by Rocker
IP 220.253.xxx.xxx
Post #529215 - in reply to msg. #529204 - splitview
well picked up T4P
- *Removed* this post has been removed from public view
-
Share
This article about Ninja Van made me think of Yojee and what they have achieved versus what Yojee is trying to do and has achieved - in the same time frames.
https://www.cnbc.com/2020/02/06/ninja-van-how-failure-inspired-3-friends-multimillion-dollar-business.html
- *Removed* this post has been removed from public view
-
Share
My understanding is that Archer had previously (circa 2015) determined that graphite at Sugarloaf was too high in carbon content for use in battery anodes, however it sounds like recent developments suggest when combined with Silicon it can actually be a very cost effective solution that can potentially also provide a higher energy density.
There are some that are developing Silicon only anode solutions, at early stages of development, and others like Altech (ATC.AX) that are coating graphite with silicon like is being suggested in this article.
Interestingly it also sounds like there are some significant Silica resources that extend from Whyalla/Port Augusta up to near Roxby Downs - search for an article on the SA Energy and Mining Website for an article titled "New Critical Minerals Opportunities". Funnily enough actually feature iTech in the article.
Utilization of impurities and carbon defects in natural microcrystalline graphite to prepare silicon-graphite composite anode for high-performance lithium-ion batteries - Published: 29 July 2021
Bei Liu, Peng Huang, Minqi Liu & Zhiyong Xie - Journal of Materials Science volume
Abstract
Impurities and carbon defects generally hinder practical application of microcrystalline graphite as anode material for lithium-ion batteries. However, the impurities and carbon defects of the natural microcrystalline graphite are found to be the active sites to catalyze silicon deposition during the chemical vapor deposition process. In this work, the impurities and carbon defects of prepared anode material are wrapped by double coatings that are combined by the silicon nanowires and the carbon layer. The composite anode material exhibits a high capacity of 640 mA h g−1 at a current density of 186 mA g−1 after 250 cycles. The results of the density functional theory calculation reveal that the existence of impurities and carbon defects on graphite surface enhances the absorption energy of graphite to silicon during chemical vapor deposition process at 900 °C. By utilizing the impurities and carbon defects, the natural microcrystalline graphite can be employed as a new and low-cost anode material to fabricate the high-performance lithium-ion batteries.
Introduction
At present, natural microcrystalline graphite is mainly used in low value-added products due to its rich reserves and low-cost, such as refractory materials [1], conductive materials [2], wear-resistant lubricating materials [3] and cast-iron additive materials. It is restricted in high value-added fields such as lithium-ion batteries (LIBs) anode materials, mainly because the impurities in graphite, which are the independent mineral inclusions and the impurity ions can replace the carbon atoms or enter the crystal lattice defects of graphite [4], resulting in the difficulty of being purified of the natural microcrystalline graphite. Besides, the abundant carbon defects appeared in the microcrystalline graphite during the processes of mining, crushing and purification have a huge impact on the performance of LIBs [5].There are two main methods for obtaining the pure natural microcrystalline graphite that can be applied in LIBs anode materials. One method is the chemical purification including acid and alkaline disposition [6]. Zhao et al. [7]. using concentrated sulfuric acid (H2SO4) and hydrochloric acid (HCl) in a thermal autoclave to purified nature graphite, followed by carbon coating. The using of general acids can effectively avoid the destructive injury to environment or human that may be brought by the hydrofluoric acid (HF) [8]. And the as-obtained natural graphite anode presented an initial coulombic efficiency of 88.4% with a capacity of 355.8 mA h g−1. As for the alkaline purification, NaOH reacts with SiO2 and Al2O3 in impurities at high temperature to form soluble salts. After filtering and washing, the purity of natural graphite can reach 99.9%. Though the natural graphite after chemical purification has a high purity, almost all countries and regions prohibit the use of chemical purification due to the huge pollution of the by-products [9]. Another method with environmental protection is the physical method [10] that mainly includes the high temperature purification. The impurities are directly volatilized by heating above the boiling point of the impurity phase with no use of any acid. After purification, the purity of natural microcrystalline graphite can reach more than 99.99%. However, the ultra-high energy consumption and high dependence on equipment lead to huge purification costs. The economical and environmentally friendly purification method of natural microcrystalline graphite needs to be addressed.
For the issue of carbon defects in natural microcrystalline graphite, surface coating is a simple and effective method to improve the battery performance [11], [12]. The surface coating method can effectively avoid the direct contact between microcrystalline graphite and the solvent thus can reduce the Li+ consumption during the formation of the solid-electrolyte interphase (SEI) [13]. And the coating layer can prevent the graphite layer from being peeled off caused by the intercalation of solvent molecules [14]. Cheng et al. [15]. fabricated electrically conductive ultrananocrystalline diamond-coated natural graphite-copper composite anode for long life LIBs. Masaki et al. [16]. reported a composite anode of spherical carbon-coated natural graphite which shows excellent battery cycle performance.
Though the natural microcrystalline graphite can be chosen as a decent anode material for LIBs by employing multiple alternative purification methods or coating it with carbon, the manufacturing cost and reversible capacity of the modified natural microcrystalline graphite still have a gap compared with the flake graphite and artificial graphite that have been commercialized. Nano-sized silicon [17] and graphite composite anode materials can simultaneously maintain the high reversible capacity of silicon and the cycling stability of graphite [18]. In Li’s work [19], a mesoporous Si/amorphous carbon/graphite composite was synthesized by high energy ball milling. Si nanoparticles and flake graphite are evolved into microspheres by self-assemble via polycondensation and surface tension of pitch. But the agglomeration of nano-sized Si and the low bonding strength between Si and graphite imply that the composite can be better modified by changing the fabrication method. The chemical vapor deposition (CVD) method is an ideal way to obtain uniform surface coating layer and realize in situ growth of materials on a target substrate [20]. Kim [21] fabricated an amorphous Si nanolayer in edge-plane activated graphite anodes surface using the CVD method employing silane as the Si source. Min Ko et al. [22]. employed silane and obtained a Si-nanolayer-embedded graphite composite for high-energy LIBs.
Herein, we using natural microcrystalline graphite ore as the raw material, after simple multiple flotation and chemical purification (general acids such as HCl, H2SO4 and other non-HF). And silicon nanowire-microcrystalline graphite composite anode was fabricated via CVD methods employing chloromethylsilane as the silicon precursor. During the CVD process, trace impurities that hard to be purified and carbon defects caused during purification processes accelerate the deposition of silicon. The utilization of impurities and carbon defects to catalyze the deposition of silicon, and the silicon can accurately cover the positions of impurities and carbon defects. As a result, the fabricated silicon-microcrystalline graphite composite anode showed an excellent battery performance. -
Share
The letter from ERM will be posted out with all voting forms to all shareholders, as per legal requirement of course, but the 3 directors letters also go, so yes, I agree that more from ERM may be required if they know they need to jolt the apathetic.
Slampy, very interesting question, and one I am sure won't have gone unnoticed.
Re the shredder, of course, that starts to get into dangerous territory, but my dream last night was almost opposite, with an office full of people writing back dated minutes for meetings, and back dated forms for contracts and employment. It was a hectic dream, and I hope there's no reality in it at all.
- *Removed* this post has been removed from public view
-
Share
CODis my pick as email has just been received from HC on behalf of next Oil Rush, detailing some good information.
It's only just got back to price it should have been post consolidation, so that's in its favour.
Very little to sell, I like that, as it will move quickly.
Many won't have received the email yet as they're at work, etc.
Read more here.
http://www.nextoilrush.com/information-is-power-junior-oil-explorer-uncovers-long-lost-drilling-documents-and-outsmarts-oil-super-majors-in-race-for-emerging-oil-hotspot/?utm_source=HCMO
Looks good for next week. Be prepared!- *Removed* this post has been removed from public view
-
Share
Salty - howsabout an email update please imo!!- *Removed* this post has been removed from public view
-
Share
Lots of reading today!
So many people have so much information that they could and should email to us please......
[email protected]
- *Removed* this post has been removed from public view
Featured News
Add to My Watchlist
What is My Watchlist?
A personalised tool to help users track selected stocks. Delivering real-time notifications on price updates, announcements, and performance stats on each to help make informed investment decisions.
|
|||||
Last
3.1¢ |
Change
0.000(0.00%) |
Mkt cap ! $5.295M |
Open | High | Low | Value | Volume |
3.0¢ | 3.1¢ | 3.0¢ | $5.171K | 171.5K |
Buyers (Bids)
No. | Vol. | Price($) |
---|---|---|
2 | 196866 | 3.1¢ |
Sellers (Offers)
Price($) | Vol. | No. |
---|---|---|
3.2¢ | 72756 | 2 |
View Market Depth
No. | Vol. | Price($) |
---|---|---|
2 | 196866 | 0.031 |
1 | 330000 | 0.030 |
3 | 590000 | 0.029 |
5 | 832130 | 0.028 |
2 | 160615 | 0.027 |
Price($) | Vol. | No. |
---|---|---|
0.032 | 72756 | 2 |
0.034 | 280000 | 1 |
0.037 | 11500 | 1 |
0.038 | 390290 | 2 |
0.040 | 91872 | 4 |
Last trade - 15.42pm 19/06/2025 (20 minute delay) ? |
|
|||||
Last
3.2¢ |
  |
Change
0.000 ( 0.00 %) |
|||
Open | High | Low | Volume | ||
2.9¢ | 3.2¢ | 2.9¢ | 92776 | ||
Last updated 13.31pm 19/06/2025 ? |
Featured News
ITM (ASX) Chart |
The Watchlist
RML
RESOLUTION MINERALS LTD
Craig Lindsay, In-Country CEO
Craig Lindsay
In-Country CEO
SPONSORED BY The Market Online