- Forums
- ASX - By Stock
- Ann: Bass to commence drilling at adjacent Mahefedok deposit-BSM.AX
GW1
greenwing resources ltd
Add to My Watchlist
4.00%
!
2.6¢
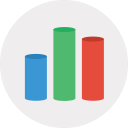
Featured News
Add to My Watchlist
What is My Watchlist?
A personalised tool to help users track selected stocks. Delivering real-time notifications on price updates, announcements, and performance stats on each to help make informed investment decisions.
|
|||||
Last
2.6¢ |
Change
0.001(4.00%) |
Mkt cap ! $7.618M |
Open | High | Low | Value | Volume |
2.5¢ | 2.6¢ | 2.5¢ | $2.664K | 102.4K |
Buyers (Bids)
No. | Vol. | Price($) |
---|---|---|
1 | 40000 | 2.5¢ |
Sellers (Offers)
Price($) | Vol. | No. |
---|---|---|
2.6¢ | 5269 | 1 |
View Market Depth
No. | Vol. | Price($) |
---|---|---|
1 | 40000 | 0.025 |
2 | 256461 | 0.024 |
2 | 850000 | 0.023 |
2 | 900000 | 0.022 |
2 | 355284 | 0.021 |
Price($) | Vol. | No. |
---|---|---|
0.026 | 5269 | 1 |
0.029 | 481596 | 1 |
0.030 | 249998 | 1 |
0.031 | 222962 | 2 |
0.035 | 979826 | 1 |
Last trade - 14.32pm 02/07/2025 (20 minute delay) ? |
Featured News
GW1 (ASX) Chart |
The Watchlist
RAC
RACE ONCOLOGY LTD
Dr Pete Smith, Executive Chairman
Dr Pete Smith
Executive Chairman
SPONSORED BY The Market Online