Interesting spiel.
I listened to it, would like to know how a pre-cast slab for a two story will work for an acceptable/desirable living area and still be able to support the upper level internal walls, say an area of 10x10m which is probably a common living area nowadays.
- Forums
- ASX - By Stock
- FBR Display home open and for sale
FBR
fbr ltd
Add to My Watchlist
8.33%
!
0.6¢
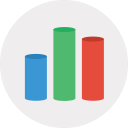
Interesting spiel.I listened to it, would like to know how a...
Featured News
Add to My Watchlist
What is My Watchlist?
A personalised tool to help users track selected stocks. Delivering real-time notifications on price updates, announcements, and performance stats on each to help make informed investment decisions.
|
|||||
Last
0.6¢ |
Change
-0.001(8.33%) |
Mkt cap ! $31.29M |
Open | High | Low | Value | Volume |
0.6¢ | 0.6¢ | 0.5¢ | $7.116K | 1.237M |
Buyers (Bids)
No. | Vol. | Price($) |
---|---|---|
138 | 55126900 | 0.5¢ |
Sellers (Offers)
Price($) | Vol. | No. |
---|---|---|
0.6¢ | 30421380 | 38 |
View Market Depth
No. | Vol. | Price($) |
---|---|---|
139 | 55127259 | 0.005 |
47 | 16679977 | 0.004 |
23 | 13670332 | 0.003 |
10 | 11803500 | 0.002 |
16 | 75071999 | 0.001 |
Price($) | Vol. | No. |
---|---|---|
0.006 | 30421656 | 38 |
0.007 | 22885546 | 31 |
0.008 | 4491612 | 9 |
0.009 | 2275330 | 4 |
0.010 | 1659259 | 8 |
Last trade - 13.32pm 02/07/2025 (20 minute delay) ? |
Featured News
FBR (ASX) Chart |
The Watchlist
RAC
RACE ONCOLOGY LTD
Dr Pete Smith, Executive Chairman
Dr Pete Smith
Executive Chairman
SPONSORED BY The Market Online