For those who may be interested in a bit more technical research, here are snippets of recent Chinese scientific research in this field.
1. Journal of Environmental Chemical Engineering Volume 12, Issue 2, April 2024, 111842 (current edition in progress)
A novel ammonium-free vanadium precipitation process for the integrated actions of ascorbic acid reduction and enhanced hydrolysis under hydrothermal influence.
Vanadium-titanium magnetite is an important source of vanadium, and V2O5 is the main vanadium product. At present, the production of V2O5 is mainly obtained by sodium salt roasting and ammonium salt precipitation, while ammonia nitrogen wastewater and NH3 discharge will cause serious environmental pollution. Calcium and iron salts are mainly intermediate products, and vanadium oxides cannot be obtained directly. Therefore, a clean and sustainable method is proposed to produce V2O5 by ascorbic acid hydrothermal reduction in one step.
When the vanadium concentration is 25.48 g/L, under the optimal vanadium precipitation conditions: the ascorbic acid addition ratio is n(ASA): n(V) = 0.1:1, the reaction temperature is 210 °C, the solution pH is 1.25, and the reaction time is 10 h, the precipitation efficiency and V2O5 purity can be 99.60% and 99.12%, respectively. The kinetics and apparent activation energy of the reaction were investigated, and the apparent activation energy was calculated to be 68.80 kJ/mol. The product obtained was characterized by XRD, SEM-EDS, XPS and FTIR, proving that the final product is V2O5. The reaction mechanism of ascorbic acid and vanadium in solution is single electron transfer and recombination, and the formation process of V2O5 is: VO3- → VO2+ → VO2 or V2O3 → V2O5, and ascorbic acid is oxidized to dehydroascorbic acid.
In conclusion, the production of V2O5 by hydrothermal reduction of ascorbic acid is environmentally friendly, clean, simple, and efficient.
Vanadium is a silver-white transition metal with a body-centered cubic lattice, which has the reputation of industrial vitamins and is one of the indispensable and important raw materials for modern industrial development [1], [2]. Vanadium has a wide range of applications. In the metallurgical industry, it is mainly used as a trace element in the production of alloy steels, tool steels, and carbon steel cast iron. Vanadium alloys can be used as high-temperature structural materials for aircraft and rockets [3]. Vanadium oxides and vanadates are used primarily in the chemical industry, such as glass, ceramics, and paints [4]. In addition, vanadium is also used in all-vanadium oxide liquid flow batteries [5].
The widespread use of vanadium poses new challenges for managing vanadium resources. Vanadium is usually associated with other metal ores in nature, and more than 70 kinds of vanadium-containing minerals have been discovered, such as vanadium titanium magnetite, vanadium potassium uranium ore, vanadium mica, vanadium lead ore, etc [6]. In addition, crude oil, coal, and oil shale also contain a large amount of vanadium [3]. South Africa, Russia, and China are the three largest producers of vanadium and 88% of the world's vanadium production is obtained from vanadium-titanium magnetite.
Vanadium in vanadium-titanium magnetite is usually recovered as V2O5 in several steps: roasting (sodium, calcium, blanks, compound additives, and sulfated roasting), leaching (direct leaching, water leaching, acid leaching, and alkaline leaching), purification (chemical precipitation, ion exchange and solvent extraction), precipitation (hydrolysis, ammonium, melamine, calcium, iron and reduction precipitation) and calcination [7], [8], [9], [10], [11], [12], [13], [14]. Among these steps, precipitation is an important step in recovering vanadium after leaching from vanadium titanium magnetite. Hydrolysis was widely used in early industrial production, and its principle was that vanadium existed in the form of polymer ions under an acidic medium, precipitated under heating and stirring, and red cakes were obtained after filtration [15]. Red cakes usually contain many impurities, while vanadium contains only about 85%. Therefore, the red cake obtained by hydrolysis needs further processing. Wang [16] studied the separation and recovery of vanadium chromium in vanadium-containing solution by hydrolysis and neutralization, and the purity of V2O5 was 98.6% after removing the sodium in the obtained sodium polyvanadate.
Ammonium precipitation of vanadium is currently the most widely used method for recovering vanadium from vanadium-containing solutions. Ammonium salts for vanadium precipitation can be divided into weakly basic ammonium salts for vanadium precipitation (pH=8.0–9.5), weakly acidic ammonium salts for vanadium precipitation (pH=4.0–6.0), and acidic ammonium salts for vanadium precipitation (pH=1.5–3.0) according to the difference of pH. Jiang [17] by adjusting the pH to 8, the vanadium precipitation efficiency by adding (NH4)2SO4 reaches 99.75%, and the purity of V2O5 after calcination reaches 95.71%. Vanadium precipitated as decavanate when ammonium salts were added to the solution at this acidity in the range of pH 4–6. Chen [18] obtained a vanadium precipitation efficiency of 99.67% and a V2O5 purity of 99.50% by adding ultrasonication to the reaction at pH 2 with NH4Cl as an additive. Ammonium salt vanadium precipitation has the characteristics of a simple process, high vanadium precipitation efficiency, and high purity of vanadium products. It is estimated that for every 1 t of V2O5 produced, 30–60 t of ammonia nitrogen wastewater is discharged, which poses a serious threat to the environment [19]. Peng [14] used melamine as the reagent for vanadium precipitation, and the vanadium precipitation efficiency could reach 99.63%, which is not only low cost but also does not produce ammonia nitrogen wastewater, but the reaction product contains toxicity. Li [20] and Liu [21] used calcium and iron salts as vanadium precipitation reagents to obtain CaV2O6 and FeO2VO(OH)0, respectively, which is a cleaner method than traditional vanadium precipitation. However, calcium vanadate prepared by calcium salt is mainly used for vanadium enrichment and as an intermediate product of ferrovanadium smelting, and cannot be used as a terminal product V2O5 [22]. The same iron salt precipitated vanadium products are not only complex in composition and low in purity, but can only be used to produce specific vanadium compounds, and cannot directly obtain V2O5. Therefore, the application of calcium and iron salts is greatly limited.
Zhang et al. [23], [24]. used hydrothermal hydrogen reduction to precipitate vanadium-rich liquid from vanadium extraction from shale to obtain V2O3 with a precipitation efficiency and purity of 99.23% and 99.83%, respectively. Similarly, Zhao [25] successfully produced V2O3 from NaVO3 by one-step molten salt electrolysis. Hydrogenation and electrolysis are not widely used due to high costs and danger.
Therefore, exploring the green and clean precipitating agents of vanadium metallurgy is of great significance.
A number of organic reagents carrying -NH2, -COOH, and -OH functional groups have been used as new vanadium precipitating reagents and have high efficiency of vanadium precipitation under specific conditions.
Ascorbic acid is a non-toxic and harmless organic reagent with reducing properties, and there is literature indicating that ascorbic acid and vanadium can undergo a reduction reaction [26]. However, there are fewer studies related to the use of ascorbic acid in vanadium metallurgy.
In addition, the hydrothermal method has been widely concerned because of its advantages of simple operation, cheap equipment, experimental large-scale production, and good crystallinity of the product.
Considering the advantages of ascorbic acid and hydrothermal method, in this study, the ascorbic acid hydrothermal reduction method was used as vanadium precipitation. This method can not only solve the environmental pollution caused by the current ammonium salt precipitation vanadium but also directly obtain vanadium oxide. The effects of ascorbic acid addition ratio (n(AsA):n(V)), reaction temperature, solution pH, and reaction time on the precipitation efficiency were investigated. At the same time, the dynamics and apparent activation energy of vanadium precipitation were analyzed. The crystal structure, micromorphology, chemical composition, valence state, etc. obtained under the optimal conditions were analyzed by XRD, SEM-EDS, ICP, and XPS. In addition, the mechanism of vanadium precipitation was explained, and the thermodynamics of the phase transition process was studied by Dmol3 and TG. This study aims to obtain a new vanadium precipitation method with low pollution, high vanadium precipitation efficiency, and high purity, and to promote the green and friendly development of vanadium metallurgy.
2. (Nov 2023)
A Novel Pretreatment Process for Vanadium Extraction:
Purification and Recovery of Negative Component Calcium in Vanadium-Bearing Steel Slag, one kind of valuable metallurgical secondary resource, can be used as an important raw material for vanadium extraction, but its high calcium content seriously affects the index of vanadium extraction. Hence, a novel pretreatment process for vanadium extraction was proposed, that is, purification and recovery of negative component calcium in vanadium-bearing steel slag.
This process included three closed-circuit procedures:
Selective calcium leaching with no extra addition of fresh leaching reagent - Rapid and efficient precipitation of calcium - Cyclic leaching of calcium precipitation filtrate without supplement of leaching after simple regeneration. After pretreatment by the novel process, leaching efficiency and acid consumption of the following vanadium leaching procedure, were significantly increased and reduced respectively. Meanwhile, the evolution of phases before and after calcium leaching were investigated via XRD and SEM-EDS, showing that the selective calcium leaching was essentially the destruction and disappearance of calcium silicate phase, while the vanadium-phase was exposed after calcium leaching, thus facilitating the subsequent vanadium leaching. Moreover, the image analysis of Ca3SiO5-H2O-NH4Cl ternary system was performed, confirming that increasing temperature could promote calcium leaching reaction, and a stable product area could be formed through ammonium chloride reacting with tricalcium silicate.
https:https://ssrn.com/abstract=4631823//ssrn.com/abstract=4631823
It would be interesting to hear comments on what makes our New Novel extraction process unique ?
- Forums
- ASX - By Stock
- SRN
- Interesting - A novel ammonium-free Vanadium precipitation process
SRN
surefire resources nl
Add to My Watchlist
50.0%
!
0.2¢
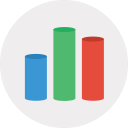
Interesting - A novel ammonium-free Vanadium precipitation process
Featured News
Add to My Watchlist
What is My Watchlist?
A personalised tool to help users track selected stocks. Delivering real-time notifications on price updates, announcements, and performance stats on each to help make informed investment decisions.
|
|||||
Last
0.2¢ |
Change
0.001(50.0%) |
Mkt cap ! $5.860M |
Open | High | Low | Value | Volume |
0.1¢ | 0.2¢ | 0.1¢ | $1.865K | 1.808M |
Buyers (Bids)
No. | Vol. | Price($) |
---|---|---|
104 | 208251358 | 0.1¢ |
Sellers (Offers)
Price($) | Vol. | No. |
---|---|---|
0.2¢ | 131098833 | 74 |
View Market Depth
No. | Vol. | Price($) |
---|---|---|
104 | 208251358 | 0.001 |
0 | 0 | 0.000 |
0 | 0 | 0.000 |
0 | 0 | 0.000 |
0 | 0 | 0.000 |
Price($) | Vol. | No. |
---|---|---|
0.002 | 131098833 | 74 |
0.003 | 36203992 | 21 |
0.004 | 22652231 | 7 |
0.005 | 4885000 | 5 |
0.006 | 3066666 | 3 |
Last trade - 15.36pm 26/08/2025 (20 minute delay) ? |
Featured News
SRN (ASX) Chart |