Dont know if this has been posted before ,but struggling to find any updates
You are here
Home » equipment » Process Extends Phosphate Reserves, Eliminates Waste
mce-anchor
Process Extends Phosphate Reserves, Eliminates Waste
October 21, 2015
0
1
2
3
The demo plant was designed to include a multi-zone AeroDry dryer from Bühler Aeroglide.
Phosphorus is essential for the biological processes of life. Phosphorus in its phosphate form is deposited in ancient, relatively shallow sedimentary basins rich with phosphate containing fossils of marine and terrestrial animals. Phosphate rock is mined and beneficiated to produce a raw material for fertilizer that farmers apply to their fields. The process begins with the excavation of a raw phosphate “matrix,” a mix of equal parts sand, clay, and phosphate mineral. Beneficiation of the matrix, consisting of washing, sizing, and flotation, makes it usable for the chemical processes needed to make fertilizer.
The phosphate in phosphate rock is insoluble in water and requires chemical modification for a plant to use it. The process for allowing the nutrient values to be liberated for plant use is called the Wet Acid Process. This process takes high-grade phosphate rock and acidulates it with sulfuric acid to make phosphoric acid and large amounts of waste phosphogypsum. The phosphoric acid is used to make fertilizers. The waste is stockpiled and managed much like a landfill.
Phosphate is a non-renewable natural resource and central Florida has the largest known reserves in the U.S. However, experts believe it could be mined out in coming decades. Finding a way to extend these reserves is important for this industry that has an estimated economic impact of $10 billion each year.
Manufacturing Phosphoric Acid
JDC Phosphate, Fort Meade, FL, has patented a new way to make phosphoric acid. JDC’s "Improved Hard Process" (IHP) will enable current reserves of low-grade phosphate rock, and wastes from previously processed rock, to be converted to usable products for agriculture and industry. As a result, IHP has the potential to nearly triple the amount of phosphate reserves available for fertilizer production in Florida. It also has the potential to eliminate the production of phosphogysum and save millions annually in landfill management costs in Florida. Globally, IHP is expected to dramatically change this industry by producing high-purity phosphoric acid from low-grade phosphate rock at a lower cost than current processing, without the high volume waste.
“We are well on the way to commercializing a breakthrough that will allow the mining of phosphate resources that haven’t been suitable for agriculture,” said JDC Phosphate’s chief executive officer Tip Fowler. “We think this will offer phosphate manufacturers a tremendous savings, not just in Florida, but globally, because of IHP’s ability to expand limited natural resources worldwide.”
JDC’s IHP was patented by Dr. Joseph Megy in 2008, and the company was founded on this propriety technology. It soon attracted investments that enabled the design and construction of a demonstration plant in 2012, to focus on demonstrating the commercial viability of IHP. Since then, validation of IHP became the focus as JDC sought to determine the particular processing parameters for phosphoric acid production.
IHP Demonstration Plant Needed Drying Expertise
Since drying was a key process requirement for IHP, JDC turned to Bühler Aeroglide for a dryer design that would be versatile enough for intermediate scale testing. Bühler also had the expertise to support equipment requirements for a full scale processing line. Prior to finalizing the demo plant design, testing was conducted at Bühler Aeroglide’s North Carolina Tech Center. JDC needed to dry an agglomerated mix of ground phosphate ore, clay, sand, petroleum coke, binder, and water to less than one percent moisture at 250°F. The mix was in the form of balls or spheres that needed to pass a number of crush tests to ensure adequate strength to maintain shape and integrity during rigorous processing downstream.
“Bringing a product to life is a journey through a variety of trials and errors,” said Bühler Aeroglide senior engineer Les Horton. “Dr. Megy had a vision that we understood and once we identified the desired product attributes, testing addressed the critical high-level requirements that thermal processing could meet.”
A multi-zone AeroDry dryer was designed and built by Bühler Aeroglide for the demo plant. It was installed after a balling-drum operation where the principle bonding mechanism was the tension of water augmented by a binder, rotating the mix to create 3/8-in. spheres. The dryer bed measured 32 x 7 ft, and could load up to 120 lb/cu ft of the ‘gunshot’-sized balls. It was designed to remove 2500 lb/hr of water from the small agglomerated spheres.
“The AeroDry gave us a robust but gentle way to dry the feed spheres after the balling drum,” said Fowler. “And we needed to find out how each formulation would hold together when it went through the remainder of the process.”
Dozens of tests were conducted to validate the drying process and each time the sphere was observed to see how it held together after drying. Researchers looked for any fines that might be created, they observed how the sphere was stabilizing and adjustments were made as needed. The demo plant dryer was designed to dry 12 tn/hr at 10% moisture. Now, the demo plant is testing IHP with product made from phosphate rock from Florida, Australia, Africa, and other parts of the world, while plant operators observe a variety of new formulations.
“For IHP to work efficiently, it’s vital that we have a continuous operation that ensures uniform drying to product specifications,” said Fowler. “When the spheres exit the dryer, they are conveyed to a rotary kiln where the spheres are heated to liberate the phosphorous gas which is converted in a conventional hydrator to phosphoric acid of high quality.”
Meanwhile, the Fort Meade demo plant is accumulating data to design larger, commercially sized plants. The demonstration plant is designed to produce an estimated 12,000 tons of phosphoric acid a year, and will provide JDC with a robust tool in its path toward full commercialization of the IHP technology. The next step is to design and construct a full-scale commercial IHP plant with a capacity between 100,000 and 200,000 tons of phosphoric acid per year, in conjunction with a licensor or project partner.
As a result, this technology holds great promise for phosphate companies to enhance and extend their operations and to continue to serve the needs of agriculture and industry. The dryer from Bühler Aeroglide combined with the collaborative nature of Buhler has given JDC the flexibility it needed to demonstrate IHP.
“We can now work with JDC to increase capacity and this means adding zone modules, adding heat and adding air flow scaled to production,” said Horton. “We are proud to be able to work with customers during testing, giving them the tools and engineering expertise to make adaptations that meet a market need.”
History of the Improved Hard Process
IHP is a follow-up to work previously conducted by Dr. Megy and his mentor, Dr. Robert Hard, while both men were working for Occidental Chemicals nearly 30 years earlier. Their efforts resulted in the patented Hard Process (named after Dr. Hard) that used heat integration to produce phosphoric acid directly from phosphate rock using a high temperature reduction reaction. The Hard Process proved to be technically viable but was not sufficiently cost effective to develop on a commercial scale.
Following a successful career as a noted scientist, engineer and entrepreneur, Dr. Megy returned to his process development roots in 2001, using his own funds and grants from the US Department of Agriculture to optimize the Hard Process. The results of his improvements quintupled throughput and resulted in the patenting of IHP. Two other patents have since been granted to Dr. Megy for IHP, and the company has further developed his technology and applied for another significant patent.
For more information on Bühler Aeroglide, visit www.buhlergroup.com/drying.
Buhler Aeroglide
- log into post comments
- Forums
- ASX - By Stock
- AEV
- JDCPhosphate
AEV
avenira limited
Add to My Watchlist
5.56%
!
0.9¢
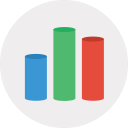
JDCPhosphate
Featured News
Add to My Watchlist
What is My Watchlist?
A personalised tool to help users track selected stocks. Delivering real-time notifications on price updates, announcements, and performance stats on each to help make informed investment decisions.
|
|||||
Last
0.9¢ |
Change
-0.001(5.56%) |
Mkt cap ! $27.00M |
Open | High | Low | Value | Volume |
0.9¢ | 0.9¢ | 0.9¢ | $2.556K | 292.7K |
Buyers (Bids)
No. | Vol. | Price($) |
---|---|---|
15 | 7834999 | 0.8¢ |
Sellers (Offers)
Price($) | Vol. | No. |
---|---|---|
0.9¢ | 808425 | 2 |
View Market Depth
No. | Vol. | Price($) |
---|---|---|
14 | 7709999 | 0.008 |
3 | 3076062 | 0.007 |
4 | 1585000 | 0.006 |
1 | 400000 | 0.005 |
2 | 1450000 | 0.004 |
Price($) | Vol. | No. |
---|---|---|
0.009 | 788425 | 1 |
0.010 | 6524872 | 13 |
0.011 | 1183224 | 3 |
0.012 | 2544954 | 2 |
0.013 | 1234269 | 4 |
Last trade - 15.55pm 11/07/2025 (20 minute delay) ? |
Featured News
AEV (ASX) Chart |
The Watchlist
VMM
VIRIDIS MINING AND MINERALS LIMITED
Rafael Moreno, CEO
Rafael Moreno
CEO
SPONSORED BY The Market Online