Hi Folks,
Here are some background information/facts from Carpentaria (CAP) about Magnetite Iron Ore...Not all magnetite ores are the same...
CAP has a very soft magnetite Iron Ore compared to its peers in WA region, something that look similar to LCY/HAW given the last DTR test results....
http://www.carpentariaex.com.au/PDF/Magnetite-Information-Sheet.pdf
MAGNETITE – WHAT YOU MAY NOT KNOW
- Magnetite is a higher grade, cleaner product than hematite
In situ magnetite ore grades are lower than commercially exploited hematite ores but after processing a product with much higher iron grades and much lower costly impurities is produced. All iron fines are recombined to form a suitable product for steel making and magnetite can be combined with bentonite (a clay) and heat to produce pellets. The high quality pellets are used in blast furnaces or Direct Reduction (DR) furnaces to make steel and is a preferred product by steel makers as they greatly increase the efficiency of the furnace, reducing costs and pollution. Magnetite and pellets attract a higher price over hematite ores for this reason.
- Magnetite is a major source for iron
In 2010 magnetite accounted for approximately 30% of global iron furnace feed for steel production. In Australia, this figure was only 3%.
- Hematite grades are dropping
In two of the major hematite exporters, Australia and India, a common theme is that the iron grade is dropping. In Australia, Macquarie Bank Research has shown that the implied grade derived for Australian exports is well below 60% as shown. This grade decrease could be due to blending lower grade ores to cash in on good prices but evertheless the evidence suggests hematite grades are dropping overall.
- Magnetite processing technologies are well understood
Given that the largest producer of iron globally uses predominantly magnetite sources and has been for many decades the magnetite processing technology is well understood and low risk. The processing flow sheets are very similar with variations generally in the crushing
and grinding circuits. A standard circuit is shown below.
The finished product is recombined and used in blast furnaces to produce steel. An important difference to the hematite product is that magnetite feed is cleaner and
importantly as magnetite gives off heat when in the furnace it therefore requires less energy to produce steel with less environmental pollutants.
- Project Valuations – not all magnetite ores are the same
To assess the value of a magnetite prospect the magnetite content and quality needs to be determined. This is done by using Davis Tube Recovery tests (DTR’s) at a laboratory scale.
This technique has been used for decades and is the standard for magnetite operations. It simulates a concentrate process by crushing, mixing with water and passing the mix over a magnet. The magnetite that is concentrated by the magnet is kept for analysis and the
residual material is rejected as tailings. The weight of the magnetite concentrate versus the original weight of the sample gives the % DTR. The concentrate sample is analysed for iron content and impurities like silica, aluminium, and phosphorous which are the most damaging impurities.
Unfortunately magnetite explorers do not always release DTR results which, makes it very difficult to compare projects. Too often just the iron head grade of the ore is released, that is the iron content in all minerals including magnetite and hematite. Only magnetite is recovered using magnets and the other iron minerals including hematite would probably be waste. It is rare that magnetite is the only iron bearing mineral in ore therefore the iron head grade is often meaningless for magnetite operations. It follows that DTR grade should
be used as the standard when reporting magnetite Mineral Resources as noted at a recent Iron Ore Conference.
The cost to process ore is very important for all mining projects and can vary greatly depending on the individual ore type. This is also true for magnetite projects. The two most important characteristics of magnetite ore that effect processing costs are grind size and hardness. The grind size is the size that the ore needs to be ground to, to release a quality magnetite product. It is generally between 150 and 25 microns (100 microns = 1 tenth of a millimetre).
More importantly the hardness of the ore determines how much power, and therefore cost, is required to reach the optimum grind size. The hardness of ore is expressed as the Bond Work Index in units of kilowatt hours per tonne (kwh/t). The smaller this number the less power used in crushing and grinding. A guide to the variability within magnetite projects is shown in the graph below from available data. The magnetite siltstones of the Braemar Iron Formation are the “softest” noted globally and have by the lowest circuit energy costs per tonne of concentrate.
Unfortunately this Bond Work Index is another number not widely released even though it is an important factor that governs a major part of the processing costs i.e. the cost of energy, electricity.
- Magnetite attracts a higher price than hematite
The additional costs in producing a magnetite concentrate are offset by the premium received due to the higher grade. For example on September 6th 2011 the spot price for:
--> 62% Iron fines – US$180.9 / dry metric tonne
--> 58% Iron fines - US$157.0 / dry metric tonne
If a 69% iron content was sold, (as expected from a magnetite concentrate), a price of US$201.3/t would be anticipated due to the additional iron. A premium of approximately US$20/t because of about 10% more contained iron. An additional premium would be received for a pellet product.
Australia has benefitted from the vast tonnages of hematite particularly in the Pilbara Region. Magnetite, however, is becoming more important as a source of high grade iron as hematite grades fall over time and iron prices remain high.
It is often stated that the typical magnetite deposit is smaller with lower margins than the hematite deposits. However combinations of very large deposits, premium prices for a better product and low cost processing mean magnetite is competitive. .....The Hawsons Iron Project is possibly becoming one competitive project where in excess of 1500 million tonnes of high grade iron concentrate could be defined and at a grade that attracts a price far in excess of the hematite resources. This is equivalent in size to the large Pilbara hematite deposits.
...The project could be very profitable long life mine using conservative engineering and financial assumptions.
The mineralised rock is very soft when compared to other magnetite iron ores providing huge cost savings in processing and the mineralisation is homogeneous which means low mining risk and high predictability in production and processing schedules..
LCY: potential future low cost magnetite producer (comparing to its peers in WA magnetite BIF projects).
From the results of DTR tests so far, LCY/HAW can take advantage and maximise the benefits of the very soft ore and excellent magnetite liberalisation...From what I can see, this will translate for LCY to be a future potential of low cost magnetite producers when comparing to its peers in WA .... A lower project cost will increase the profit margins/revenues, Internal Rate of Return (IRR) and the NPV...
From LCY's ann 20/01/2012: LCY: EXCELLENT METALLURGICAL RESULTS
Outstanding metallurgical test work results highlight a relatively soft magnetite with low Bond Work Index, high weight recovery and coarse grind for premium concentrate,low power costs.
Metallurgical Test Work
Comprehensive metallurgical test work has been undertaken on the Mt Bevan magnetite mineralisation supervised by Calibre Global. This includes routine DTR testing on 6m
composites (based on grind liberation curve test work tailored to the mineralisation), LIMs testing, and Bond Work Index test work. DTR testing of mineralisation intersected in phase 2 drilling has produced very similar results to that of previous drilling. Using a relatively coarse grind size of P80/50 – 55 microns, DTR testing shows excellent achievable grades of 69 – 70% Fe and with high weight recoveries of circa 45%. Silica contents at this relatively coarse grind remain low, averaging 3 - 4 % with very low sulphur and phosphorus.
These outstanding results place the Mt Bevan magnetite resource at the highest quality level of West Australian magnetite projects, particularly in the low silica component of the concentrate. Most peer projects show DTR concentrate silica in the 4.5% to 6% range and utilise a more costly finer grind. Put simply, even with a lower cost coarse grind size, Mt Bevan magnetite can produce a premium concentrate with low silica. Importantly, there is also no necessity for a flotation circuit as is common for many WA magnetite projects.
The DTR results indicate that a high purity magnetite concentrate can be produced. This gives the project the potential flexibility to produce either normal BF (Blast furnace) grade pellets (silica < 5.5%) which may be produced at a coarser grind size, or premium DR (Direct reduction) grade pellets (silica < 3%) at a finer grind size.
Low Grinding Costs
Comprehensive testing on diamond core samples by Ammtec has provided a Bond Work Index of 11kWh/t. This is relatively soft for magnetite BIF mineralisation. In comparison, most WA magnetite BIF projects have a Bond Work Index of circa 18 – 20 kWh/t.
Low Operating Costs
The combination of being able to produce a quality concentrate at a relatively coarse grind and the soft nature of the mineralisation has a very significant positive economic impact for a mining project at Mt Bevan. A major OPEX cost in magnetite projects is power consumption. Preliminary energy calculations based on the grind and bond work index indicate power requirements of only 12 kWh/t – very low compared to that of about 30 kWh/t for typical WA magnetite projects.
Sharon Heng: “These drilling and metallurgical test work results are outstanding as they not only point to low mining costs but also to low processing costs producing a premium grade product which has the real potential to underpin extremely attractive project financials. With NMDC’s confirmed support, we look forward to rapidly developing the project this year with on-going drill programs, testwork and studies”.
DYOR,
Cheers
- Forums
- ASX - By Stock
- LCY
- lcy: future low cost magnetite producer
LCY
legacy iron ore limited
Add to My Watchlist
0.00%
!
0.9¢
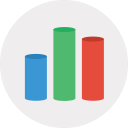
lcy: future low cost magnetite producer
-
- There are more pages in this discussion • 28 more messages in this thread...
You’re viewing a single post only. To view the entire thread just sign in or Join Now (FREE)
Featured News
Add to My Watchlist
What is My Watchlist?
A personalised tool to help users track selected stocks. Delivering real-time notifications on price updates, announcements, and performance stats on each to help make informed investment decisions.
|
|||||
Last
0.9¢ |
Change
0.000(0.00%) |
Mkt cap ! $87.85M |
Open | High | Low | Value | Volume |
0.9¢ | 1.0¢ | 0.9¢ | $8.726K | 937.8K |
Buyers (Bids)
No. | Vol. | Price($) |
---|---|---|
1 | 11938 | 0.9¢ |
Sellers (Offers)
Price($) | Vol. | No. |
---|---|---|
1.0¢ | 580198 | 4 |
View Market Depth
No. | Vol. | Price($) |
---|---|---|
1 | 11938 | 0.009 |
8 | 3736836 | 0.008 |
9 | 2170947 | 0.007 |
2 | 266666 | 0.006 |
1 | 179888 | 0.004 |
Price($) | Vol. | No. |
---|---|---|
0.010 | 455198 | 3 |
0.011 | 1850252 | 6 |
0.012 | 283172 | 3 |
0.013 | 100000 | 1 |
0.015 | 555555 | 1 |
Last trade - 15.09pm 18/07/2025 (20 minute delay) ? |
Featured News
LCY (ASX) Chart |