Fort Meade company aims to transform global phosphate production
http://www.theledger.com/news/20161...aims-to-transform-global-phosphate-production
FORT MEADE – A local start-up company is sitting on technology that could transform the global phosphate fertilizer industry.
It just needs to raise another $10 million from investors to prove it works.
“This is a turnaround new technology in a transformational age of new technologies,” said Theodore “Tip” Fowler, chief executive officer at JDCPhosphate in Fort Meade. “We all believe we have an opportunity to change an industry in a positive way.”
The new technology is called the “Improved Hard Process” – originally named not for its level of difficulty but after Robert Hard, a chemical engineer who developed the process in the 1980s.
The late Joseph Megy, one of Hard’s colleagues and a founding partner with Fowler at JDC, is the person who improved the original Hard Process. He died in May 2015 while refining the improved process.
“The reason we’re all here is we have the opportunity to change an industry globally – not just in Florida, globally,” said James Trainham, who succeeded Megy as JDC’s chief technology officer. “It (the improved process) changes the whole supply chain.”
The Improved Hard Process manufactures phosphoric acid, the key ingredient in phosphate fertilizers, from phosphate ore. It makes significant improvements over the current technology, called the “wet acid process,” used in global phosphate fertilizer manufacturing.
One major benefit of the new technology is that it doesn’t create environmentally hazardous phosphogypsum, or gypsum.
The radium in gypsum makes it slightly radioactive, rendering the gray, powdery substance unusable for any kind of commercial byproduct. As a result, it must be stored in large, hilly structures called gypsum stacks, usually near a phosphate fertilizer plant.
That benefit became particularly relevant last month, when a sinkhole opened up underneath a gypsum stack at the Mosaic Co.’s New Wales fertilizer plant south of Mulberry. The sinkhole swallowed about 215 million gallons of contaminated water from a pond on top of the stack, an accident that Mosaic officials acknowledged could cost up to $50 million to clean up.
The accident also has become a public relations disaster for Mosaic, which delayed telling the public about it for nearly three weeks. Residents near the plant protested that the gypsum stack water could contaminate their drinking wells, which Mosaic officials say is unlikely.
Florida currently has 24 gypsum stacks with more than 1 billion tons of phosphpgypsum, according to Florida Industrial and Phosphate Research Institute in Bartow. Companies add about 30 million tons of new gypsum to the stacks annually.
“The logical question is: Is there a process that doesn’t produce phosphogympsum?” Fowler said.
Another proven benefit of the improved process is that it can manufacture phosphoric acid from low-grade phosphate rock reserves that can’t be used by the current technology, Fowler said.
That could dramatically extend the life of Florida’s phosphate reserves, which by some estimates will be exhausted in 30 to 40 years, said Fowler and Brian Birky, executive director of the Phosphate Research Institute. The institute has worked with JDC over the past several years.
Mosaic’s current corporate strategy calls for it to extend phosphate mining gradually from current locations around Polk County south into Hardee and DeSoto counties.
But the company can mine only high-grade ore reserves just below the surface, Birky said, because the wet acid process can’t handle the low-grade reserves farther down.
“If you’re looking at 30 to 40 years of mining with the upper level material, you could easily double that by mining the material below,” he added.
Birky also agreed with Fowler the Improved Hard Process manufactures a purer grade of phosphoric acid that would produce more and better fertilizers.
The new technology also would reduce the cost of manufacturing the higher quality phosphoric acid by 20 percent, Fowler said.
Birky, a public and environmental health researcher, had no opinion on production costs. But he added there’s reason to believe the improved process would be cheaper, mainly in that it uses less water and comes with fewer environmental costs associated with maintaining and monitoring gypsum stacks.
Having overcome many obstacles in eight years since JDC’s founding, the Improved Hard Process faces one last hurdle: Proving the technology can operate continuously over an extended period of time.
“We’re making the assumption that after six months of continuous production, we’ll have enough confidence in the production data to scale up,” said David Blake, vice president of operations and engineering.
The demonstration plant has an annual production capacity of producing 12,000 tons of phosphoric acid. A viable commercial plant would need to produce at least 200,000 tons a year, Trainham said.
That’s where the additional $10 million in new investment comes in.
JDC raised about $50 million so far to build and operate its first demonstration plant, which began production in 2013, Fowler said. Since then, it has run only in short spurts, the longest almost two months, because technical problems arose.
The biggest problem was the accumulation of dust in the kiln that’s the central part of the process, he said. The dust clogged up the system.
“That was a problem that, if we didn’t solve, we were toast,” Fowler said. “If we didn’t solve that, we didn’t have a process.”
Fowler credited Blake and Trainham with solving the dust problem. Blake began as a consultant in November 2013 and joined JDC full time the following May, and Trainham joined the company in June 2014.
But the solution involves installing a second production kiln and other equipment at a cost of more than $10 million, the JDC officials said.
Once the money is raised, it would take about a year to install the new equipment, followed by several months of testing, then continuous production, Fowler said.
After JDC demonstrates the Improved Hard Process is a viable and economical technology, plans call for licensing it to companies interested in building a full scale commercial plant, the officials said.
A full scale plant would probably take three to five years to build, Blake said.
“It’s not a process for tomorrow,” Fowler said. “It’s a process for a number of tomorrows.”
- Forums
- ASX - By Stock
- AEV
- new jdc article
AEV
avenira limited
Add to My Watchlist
5.56%
!
0.9¢
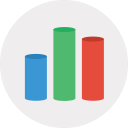
new jdc article
Featured News
Add to My Watchlist
What is My Watchlist?
A personalised tool to help users track selected stocks. Delivering real-time notifications on price updates, announcements, and performance stats on each to help make informed investment decisions.
|
|||||
Last
0.9¢ |
Change
-0.001(5.56%) |
Mkt cap ! $27.00M |
Open | High | Low | Value | Volume |
0.9¢ | 0.9¢ | 0.9¢ | $2.556K | 292.7K |
Buyers (Bids)
No. | Vol. | Price($) |
---|---|---|
15 | 7834999 | 0.8¢ |
Sellers (Offers)
Price($) | Vol. | No. |
---|---|---|
0.9¢ | 808425 | 2 |
View Market Depth
No. | Vol. | Price($) |
---|---|---|
14 | 7709999 | 0.008 |
3 | 3076062 | 0.007 |
4 | 1585000 | 0.006 |
1 | 400000 | 0.005 |
2 | 1450000 | 0.004 |
Price($) | Vol. | No. |
---|---|---|
0.009 | 788425 | 1 |
0.010 | 6524872 | 13 |
0.011 | 1183224 | 3 |
0.012 | 2544954 | 2 |
0.013 | 1234269 | 4 |
Last trade - 15.55pm 11/07/2025 (20 minute delay) ? |
Featured News
AEV (ASX) Chart |
The Watchlist
VMM
VIRIDIS MINING AND MINERALS LIMITED
Rafael Moreno, CEO
Rafael Moreno
CEO
SPONSORED BY The Market Online