Thanks very much, you're a star!
- Forums
- ASX - By Stock
- TON
- Panasonic - All Aboard
TON
triton minerals ltd
Add to My Watchlist
10.0%
!
0.6¢
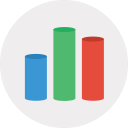
Panasonic - All Aboard, page-5
Featured News
Add to My Watchlist
What is My Watchlist?
A personalised tool to help users track selected stocks. Delivering real-time notifications on price updates, announcements, and performance stats on each to help make informed investment decisions.
|
|||||
Last
0.6¢ |
Change
0.001(10.0%) |
Mkt cap ! $8.626M |
Open | High | Low | Value | Volume |
0.6¢ | 0.6¢ | 0.6¢ | $28 | 5K |
Buyers (Bids)
No. | Vol. | Price($) |
---|---|---|
2 | 349847 | 0.5¢ |
Sellers (Offers)
Price($) | Vol. | No. |
---|---|---|
0.6¢ | 3428869 | 7 |
View Market Depth
No. | Vol. | Price($) |
---|---|---|
2 | 349847 | 0.005 |
7 | 2700192 | 0.004 |
5 | 2869995 | 0.003 |
3 | 1550000 | 0.002 |
4 | 6100000 | 0.001 |
Price($) | Vol. | No. |
---|---|---|
0.006 | 3428869 | 7 |
0.007 | 541944 | 3 |
0.008 | 1325790 | 2 |
0.009 | 781579 | 2 |
0.010 | 1500000 | 1 |
Last trade - 15.17pm 04/07/2025 (20 minute delay) ? |
Featured News
TON (ASX) Chart |
The Watchlist
NUZ
NEURIZON THERAPEUTICS LIMITED
Dr Michael Thurn, CEO & MD
Dr Michael Thurn
CEO & MD
SPONSORED BY The Market Online