OK Guys - the time has come PFS in the cue for release by ASX
so in the meantime consider this - some banter going around at present about flake size specifically for the EV battery market ( we have a range of J/SJ/LARGE as well as smaller ) so lets take a look at this so we can gain more knowledge on the subject - some person's believe VRC dont have the right stuff hence some some statements floating around on other threads so - dont ask me who - its not my policy to call people out - anyway it went something like this -
1) "Jumbo and SUPER JUMBO CATEGORY are not a measure of "purity"
for example, VRC have 910ppm of vanadium in their ore, which is an IMPURITY
regardless of the VRC flake size, the impurity must be cleansed
2) flake size is important for certain graphite uses, such as for "refractories"
for the battery market, flake size is not important"
*** Guys N Gals Im all for being objective - so i decided to do more research and i came up with the information below - ill leave it up to you experts to decide for yourselves
Comments :
number 1 above - could it be that our imputities have indicated a higher cost per tonne because of the higher levels of Vanadium or are we ok and the person who made the statement is talking #%^^Also dont forget the resource is close to surface resource which claws back project cost even if we have higher than normal level of impurity ? So sure, if so then we have to cleanse the impurities to obtain our 99.8% purity so what right??? might add to cost per tonne somewhat - Remember project cost is key to profit margins and IRR % -
Important note:Battery-grade graphite requires very high purity levels, typically >99.9% carbon-as-graphite (Cg). This material also needs to be spheroidized using careful processes that convert the flat graphite flakes into potato-like shapes, which pack much more efficiently into a given space.
The high purity levels and the enhanced "tapping" density (to >0.9 kg/m3) are important for producing the high electrical conductivity that is required during anode operation.
Reference to Number 2 comment above- the all important flake size argument "flake size" - lol
Spheroidizing the graphite flakes also reduces their size, a process known as micronization. Standard battery-grade materials require an average diameter of approximately 10-30 μm, so in theory, feedstock materials with flake sizes greater than 30 μm (+400 mesh) could be used. However, starting purity levels tend to decrease with flake size, so flake material with an average diameter of 150 μm (+150 mesh) or greater is typically used. This is, of course, a double-edged sword, since the larger the flakes used, the more energy will be required to reduce the average size of the flakes to the desired 10-30 μm.
Smaller particles are preferred, as this makes it easier for the lithium ions in the electrolyte to diffuse between graphite particles.
It should be noted that it is the tendency for purity levels to increase with flake size that is the real reason for the common 'mantra' that for battery-grade materials, the bigger the flake size, the better. In fact, the ideal precursor material would have small flake size if it had sufficient purity levels for the subsequent processing to be cost-effective.
Cheers G101 - bring on the PFS and we will all know alot more - remember each graphite resource can be different in chemical structure and very few will get to EV market - now why so much selling recently - we will find out !! - markets are a risky place for the uneducated so lets get educated fast !!!!
More information to consider on the subject of flake size for battery EV market
.......
The graphite may be purified before or after spheroidizing and micronizing, depending on the manufacturer. As mentioned earlier, the low-cost approach typically used in China is to leach the impurities from the graphite with acid, with the associated environmental concerns that that brings. Alternatively (and far more acceptable in Western jurisdictions), a thermal process can be applied. This typically involves the use of halogen gases to cause chemical reactions at high temperatures with the impurities, which covert the resulting compounds into gases too and eliminate them from the bulk graphite material.
The higher the starting purity levels of the graphite after initial concentration at the mine site, the lower the cost will be for purification, and this can make a substantial difference when comparing concentrate feedstocks with different starting purity levels. TMR estimates that the cost difference in purifying a 95% Cg concentrate to >99.9% Cg, versus taking a 98% Cg concentrate to >99.9% Cg could be as much as $2-3,000/t of concentrate, using thermal processes.
The final step for preparing spheroidal graphite for anode production is the application of a coating to the particles to reduce their specific surface area. This is important, as reducing the specific surface area will increase the long-term capacity of the battery cell. Intercalation of the electrolyte solvent into the graphite and its reaction with it causes expansion of the graphite, with the potential for delamination and a lowering of the life expectancy.
During the first charge of the battery cell, an initial, irreversible chemical reaction occurs between the electrolyte and the graphite in the anode, resulting in the formation of a so-called surface electrolyte interphase (SEI) layer. Once formed, this layer reduces further decomposition of the electrolyte and actually protects the graphite anode from exfoliating.
With too large a specific surface area, the formation of the SEI layer can reduce the graphite's ability to subsequently hold and to release the lithium ions in the electrolyte, thus reducing lifetime capacity for the battery. Coating the graphite prior to anode production reduces this effect and helps to maintain the maximum capacity possible for the battery. The coating can also reduce the chances of a runaway chemical reaction in the battery.
http://www.techmetalsresearch.com/2014/03/going-natural-the-solution-to-teslas-graphite-problem/
- Forums
- ASX - By Stock
- VRC
- PFS - When?
VRC
volt resources limited
Add to My Watchlist
0.00%
!
0.4¢
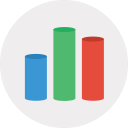
PFS - When?, page-80
You’re viewing a single post only. To view the entire thread just sign in or Join Now (FREE)
Featured News
Add to My Watchlist
What is My Watchlist?
A personalised tool to help users track selected stocks. Delivering real-time notifications on price updates, announcements, and performance stats on each to help make informed investment decisions.
|
|||||
Last
0.4¢ |
Change
0.000(0.00%) |
Mkt cap ! $18.73M |
Open | High | Low | Value | Volume |
0.4¢ | 0.4¢ | 0.4¢ | $1K | 250K |
Buyers (Bids)
No. | Vol. | Price($) |
---|---|---|
31 | 41880460 | 0.3¢ |
Sellers (Offers)
Price($) | Vol. | No. |
---|---|---|
0.4¢ | 1374594 | 8 |
View Market Depth
No. | Vol. | Price($) |
---|---|---|
31 | 41880460 | 0.003 |
10 | 14758846 | 0.002 |
7 | 32205000 | 0.001 |
0 | 0 | 0.000 |
0 | 0 | 0.000 |
Price($) | Vol. | No. |
---|---|---|
0.004 | 848817 | 5 |
0.005 | 14186051 | 16 |
0.006 | 5853903 | 7 |
0.007 | 6668572 | 3 |
0.008 | 1340000 | 3 |
Last trade - 09.59am 11/07/2025 (20 minute delay) ? |
Featured News
VRC (ASX) Chart |
The Watchlist
VMM
VIRIDIS MINING AND MINERALS LIMITED
Rafael Moreno, CEO
Rafael Moreno
CEO
SPONSORED BY The Market Online