Pumped about the future
1 June 2016 / Brent Balinski
Source: manufacturers' Monthly
Recent Endeavour Awards champion Admedus is growing briskly, with their tissue engineering process being used to repair hearts all over the world. Brent Balinski spoke to the company’s chief operating officer, Dr Julian Chick.
Australia’s “clean and green” image is a benefit well-known to many of our food exporters.
Regulations are among the reasons it’s enjoyed, and have helped keep things like bovine spongiform encephalopathy (BSE or Mad Cow Disease) out of the country.
Strict regulations are also beneficial for medical technology companies such as Admedus, which last month took out the Manufacturer of the Year and Most Innovative trophies at this magazine’s Endeavour Awards.
“I think people don’t understand or fully appreciate that, perhaps, in Australia – this whole bio/national security [advantage],” Dr Julian Chick, chief operating officer of Admedus, told Manufacturers’ Monthly.
“Australia is unique, along with a couple of other countries, in the sense that we are BSE-free. We are free of a lot of the other viruses, the prions and various other diseases that are seen around the world, and so the location is great for sourcing material.”
The material in question, for Admedus, is bovine pericardium - membranous tissue harvested from cow hearts, specially treated, and used in life-saving operations. Disease-free cows are essential.
The company’s flagship CardioCel product was released in 2013 and adoption has been rapid. It is now used in over 145 centers worldwide.
Last year the company announced results of a study of 11 long-term patients (all of whom had an implant for five years or longer.) It found no evidence of calcification, a big problem for competing implants, and there had been no need in any of the 11 for follow-up surgery.
By a lot of measures, it has been a successful invention.
“You look at the first patient that had CardioCel implanted into them - this is a three-week old child that needed life-saving surgery and was probably facing multiple surgeries over the first ten years of their life,” explained Chick.
“They’re now over eight, have never had repeat surgeries, have a good, healthy condition, and are leading a normal life.”.
According to the ASX-listed company’s count, implants of the single-ply bioscaffold - made using the company’s ADAPT tissue engineering process - totalled over 50 in December 2013, 1,100 in December 2014, 3,100 in December last year, and topped 4,000 in March.
Admedus opened its manufacturing facility in Malaga in August 2014. Its quality management system is based on ISO 13485.
It currently employs around 20 directly in production and another 30 indirectly. It is “pretty much a science-trained workforce”, said Chick.
“The skillset within the organisation does vary across the board, but we do have everything from top medic and bio-engineering background folks, senior scientists, right through to regulatory and quality assurance people that are pivotal to that manufacturing process.”
It can be done in Australia
The tissue engineering process involves sourcing the raw material, treating this in special detergents and removing all DNA, RNA and animal cells, stimulating protein-protein interactions, and encouraging strength and elasticity in the patches.
“At the moment is sold as a flat product. Imagine a business card,” explained Chick, adding that the company is in the middle of efforts to grow its range of solutions.
“And we have that but we have the ability to shape that in the shape of - if you imagine a half a pipe or a bit of plumbing material. But that’s particularly for vascular surgeons.”
CardioCel is part of the regenerative medicine division of Admedus, with the other area of focus in immunotherapies. This includes commercialising Herpes Simplex and Human Papillomavirus vaccines (currently in clinical studies) with Professor Ian Frazer (inventor of Gardasil, made by CSL).
Longer-term efforts in regenerative medicine include using tissue created by ADAPT to deliver stem cell therapies. Implants for repair of dura mater (a lining of the brain and spinal cord that can be damaged in traumatic injuries) are currently being tested.
The method of engineering biomaterials came from and was led by Professor Leon Neethling, whose bio includes opening the world’s first heart valve bank, in South Africa, in 1984.
A small amount of CardioCel implants were made, prior to Admedus’s factory opening in 2014, at Royal Perth Hospital.
European approval took place in 2013 and in the US the year after, with the first shipment also taking place in 2014. Since the launch in 2013, the range of products based on ADAPT has grown to six.
The journey from raw technology through labs and trials to product took roughly 10 years, said Chick.
“And it’s a good example of it being able to be done in Australia,” he added.
Chick, who has a PhD in muscle physiology and a background in investment banking as well as diagnostics and healthcare companies, has strong feelings about what could be done to better encourage the commercialisation of promising raw technologies.
“It’s a bit of a hobby horse of mine,” he said, adding that the issue is an old one and spans a lot of different industries.
It is one particularly strongly felt in medical manufacturing, with many ideas floated in the last few years - often around taxation rates - about how production can be kept here.
Though the Australian environment has its pluses - including around biosecurity - there’s a need to do better on a number of fronts to keep the benefits of locally-created IP here, said Chick.
Again, Admedus collaborator Ian Frazer comes up.
“Look at Gardasil - that’s a product that sells $US2 billion a year,” says Chick.
“It was invented here in Australia and Australia gets about $100 million of that $2 billion, a small per cent of the returns on that product. And if you talk to Ian, in all honesty, he’d say it would’ve been greater if we could’ve kept that in Australia for longer.
“So I think greater collaborations for B to B, academia, organisations to industry, and anything we can do to support that - that to me is the key.”
- Forums
- ASX - By Stock
- Pumped About The Future
AVR
anteris technologies global corp.
Add to My Watchlist
7.92%
!
$5.18
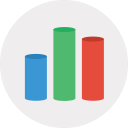
Pumped about the future 1 June 2016 / Brent Balinski Source:...
Featured News
Add to My Watchlist
What is My Watchlist?
A personalised tool to help users track selected stocks. Delivering real-time notifications on price updates, announcements, and performance stats on each to help make informed investment decisions.
|
|||||
Last
$5.18 |
Change
0.380(7.92%) |
Mkt cap ! $80.31M |
Open | High | Low | Value | Volume |
$4.85 | $5.18 | $4.85 | $39.09K | 7.832K |
Buyers (Bids)
No. | Vol. | Price($) |
---|---|---|
2 | 1200 | $4.90 |
Sellers (Offers)
Price($) | Vol. | No. |
---|---|---|
$5.18 | 2066 | 1 |
View Market Depth
No. | Vol. | Price($) |
---|---|---|
1 | 1000 | 4.900 |
1 | 2000 | 4.880 |
1 | 209 | 4.780 |
1 | 1000 | 4.700 |
1 | 2134 | 4.680 |
Price($) | Vol. | No. |
---|---|---|
5.190 | 5000 | 1 |
5.200 | 136 | 1 |
5.350 | 55 | 1 |
5.490 | 112 | 1 |
5.500 | 1886 | 2 |
Last trade - 16.10pm 18/07/2025 (20 minute delay) ? |
Featured News
AVR (ASX) Chart |