Why the metal becomes more and more important
Runon the "white gold" of ore and geothermal
Lithium from Germany

Lithium is one of the most popular raw materials in the modern world – and one of Europe's largest populations is in Germany. For a long time, the dismantling of the $8222; white gold in the upper Rhine digging and in the Erzgebirge was not profitable, but that has changed. New procedures and rising lithium prices make local lithium production attractive. First pilot projects are already running.
80 percent of the currently funded worldwide are currently from only a handful of countries. Germany has so far also been completely dependent on lithium imports. In a way that could help to obtain lithium from local resources, and that in a much more sustainable way than in the classic extraction methods. But how does the lithium come from the ground? And how rewarding is the dismantling on the upper Rhine and in the Erzgebirge
Indispensable lithium
Lithium is considered the new „White Gold, because the alkali metal is needed more urgently than ever, with the boom of mobile electronics, electric power and the need for energy storage for renewable energy, demand for the raw material is growing rapidly. According to EU forecasts, Europe alone could need around 60 times as much lithium by 2050 as much as today.
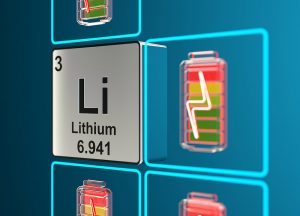
Energy turn drives lithium hunger
The main reason for this development is Lithium-ion-akkus energy suppliers for almost all mobile applications. Because of their high energy density and good restability, these batteries have so far been essential, even if already To alternative is being investigated. In 2016, according to the German Rohstoff Agency (DERA), the share of the global lithium required for these batteries was only around 38 percent of the total demand, followed by around 25 percent for the ceramic and glass industry, in which lithium is used as a river and for hardening. In 2021, the share of battery production was already more than 70 percent.
The biggest driver for this development is the electric mobility of importance – the automotive industry is increasingly converting to e-vehicles. On average, around 10 to 12 kilograms of lithium are needed for the battery of an electric car. The raw material needs are increasing rapidly – also in Germany. According to estimates by the Öko Institute in 2030, the major German car companies and the factories for batteries planned in Germany could need up to 160,000 tonnes of lithium in 2030, almost twice the entire world-year production on this raw material.
Future demand exceeds current amounts of funding
According to the German Rohstoff Agency, the global lithium funding quantity was around 82,000 tonnes in 2020. However, only half of them were so-called „Battery Grade lithium salts with less than 0.5 percent contamination by other metals, and an increase in the support of three to six times will be necessary to meet global needs, according to DERA.
The increasing demand brings another problem: Lithium has been becoming more and more expensive for years. In 2021, with an increase of 240 percent, even a regular price explosion. Experts expect this trend to continue with the increasing competition for this raw material. For the moment, demand forecasts and conveyor amounts are still still emerging.
Germany is also lithium rich
But there is no shortage of lithium deposits worldwide: according to the US Geological Survey, global resources comprise at least 86 million tonnes. Of this, in the „Lithium triangle between Bolivia, Chile and Argentina alone, together with almost 50 million tonnes of white gold, another 6.4 million tonnes stored in the underground of Australia and well five million tonnes are found in China.
Germany is also good in terms of Lithium: with an estimated 2.7 million tonnes, there are even the largest resources of the metal across Europe. They focus on the upper Rhine dig, in the ore and in the deep waters of northern Germany. Nevertheless, these lithium resources have not been used so far, Germany is still almost a hundred percent of the lithium import.
The reason for this is the type of lithium resources and their extraction.
From raw material to lithium salt
The long way to the battery
Lithium never occurs as a pure metal because of its high response joy, but only in the form of lithium salts. These can be found as minerals in Erz deposits, on the other hand, solved in the salt-containing brine of salt lakes, hydrothermal deep waters or the aqueous mixes of oil reserves. The world-funded lithium currently comes from brine and half from solid rock.
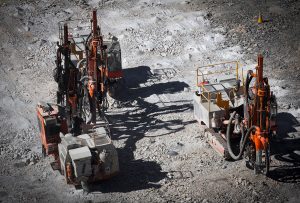
How feasible and profitable the production of lithium from such resources is depends on both the lithium content of the brines and the other composition of raw materials. Because the more contamination in the form of other alkali and alkalkaline metals the material contains, the more expensive the preparation is. These aspects are also that made German lithium deposits seem to be competitive for a long time. The promotion of purer and more rich resources has been more profitable elsewhere – so far
From ore to battery raw material
The largest reduction of lithium-containing ore is currently taking place in Australia, which delivered well half of the world's manufactured Lithium in 2021. The most common mineral Spodumen (LiAlSi2O6contains up to 3.7 percent lithium and relatively little disturbing mixing. The rock, partly underground, partly underground, is initially grind, dried and concentrated by magnetic and heavy-related methods.
However, in order to obtain battery raw material in the form of the salts of lithium carbonate and lithium hydrooxide, this raw concentrate must be prepared by heat and chemical solvent in a multi-scribitor process. According to the German Rohstoff Agency (DERA), the process chemicals required for this account for around 43 percent of the total cost.
However, this preparation for lithium from solid rock is usually not in the country, but almost exclusively in Asia. The currently largest producer of battery raw materials in the form of processed lithium carbonate or lithium hydrooxide is China, according to DERA. Apart from the economic risks of such a quasi-monopoly position, this also means that the lithium for accumulation is representing enormous transport routes $8211; a factor that has a negative impact on the climate balance of batteries.
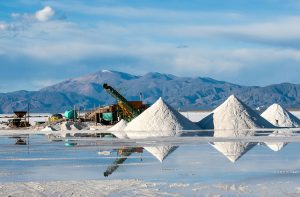
Made from brine
The second way to use lithium is to be extracted from salt-containing water. This dissolved lithium is currently being promoted mainly from the large salts in the South American lithium triangle in Chile, Argentina and Bolivia. But also in China, some lithium-containing brine deposits are already being used. The lithium content of these waters is between a few hundred and more than a thousand milligrams per litre. The highest is the concentration at around 1,570 milligrams per litre in the Chilean salt lake Salar de Atacama.
The great advantage of lithium production from the salt lakes: much of the necessary work is done by the sun, which makes the salt silk evaporate and concentrated. The water is guided by a number of evaporation pools in which, using different chemicals, foreign metals are excluded as salts, and remains a cleaned solution from which, ideally, can be obtained high-purity nitrium chloride or directly battered lithium carbonate.
The great disadvantage, however, is that enormous amounts of water are consumed for this process, and that in one of the most dry regions on the world. The production of a ton of lithium salt requires on average around two million tonnes of water. And it also takes a lot of time: from the introduction to the first pool to the finished lithium carbonate or lithium chloride, it can take up to 18 months. In addition, this so far-common form of lithium production from brine is not efficient because on average only around 60 percent of the raw material contained in the brine can be separated, the rest is pumped back unused with the waste water.
Is the change coming?
Despite the disadvantages, these classic forms of lithium production from ore or brine have so far been dominant because economically the most lucrative. The most of the world's lithium production is therefore due to these production methods and regions. But with increasing demand and rising lithium prices, the use of further resources currently as non-competitive resources are also focused 蝷 and this includes German lithium deposits.
Abbau of tin water as a source of raw material
Lithium from the Orke
Although Germany currently covers its entire lithium requirements through imports – there would be plenty of white gold. After all, 2.7 million tonnes of lithium resources could slump in the German ground, according to current estimates by the US Geological Survey.
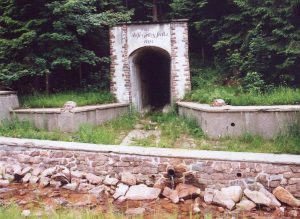
tin forest and its mineral
One of these deposits is located under the eastern ore near Zinnwald. There were already a decade ago, cin and wolf-containing ore. The fact that the gland minerals there also contain lithium, the chemist Martin Heinrich Klaproth found in 1810. He published the first analysis of the lithium emission glimmer mentioned after this finding. In the 1920s, smaller amounts of the lithium-containing mineral were temporarily dismantled in Zinnwald.
Because the rather soft, leafy silicon ineral but only contains 0.92 to 1.85 percent lithium and occurs in the rock of the storage mixture with other minerals, the dismantling was not worthwhile for a long time. When the ore reduction in Zinnwald was ended about 75 years ago, the lithium deposits there were also forgotten. Only in the last ten years, the storage has been brought back into focus in the face of rising world market prices of Lithium.
The German Lithium company has conducted new analyses, according to which the tin forest supply contains around 125,000 tonnes of metallic lithium alone on the Saxon side of the Erzgebirgrgrge. This corresponds to around 650,000 tonnes of lithium carbonate and „would be enough to equip around 20 million electric cars such as ID.3, explains Armin Müller of Deutsche Lithium
Abbau could become profitable
However, the lithium mercence must be removed and cleaned up half-time. According to a company's feasibility study, which was created in 2019, an underday dismantling of around 570,000 tonnes of ore a year, an economic operation could be made for more than 30 years $211; unless the price of lithium on the world market. According to German Lithium, the lithium carbonate gained in tin forest is unlikely to be more expensive than the lithium sales from Australian mines.
However, investments of a total of around 160 million euros would be necessary. However, German Lithium emphasises the advantages of local promotion of the raw material: „A major advantage in this project is that the lithium storage is not in a distant place, but in the heart of an industrial region, close to potential customers and partners, says Müller. This makes long transport routes unnecessary and thus also saves CO2.
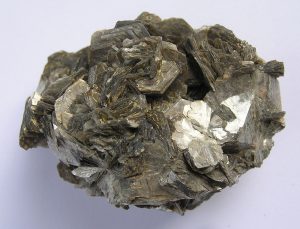
First grinding and separation…
In order to gain lithium carbonate as efficiently as possible from the Erzgebirgrgrgebnis, scientists from the Technical University of Freiberg have developed a process adapted to tin forest geology. This is used to make the tin forest alongside lithium and potassium contains relatively much iron, which makes the mineral magnetic. The side rock quartz does not contain iron. This makes it possible to break up by means of magnetic decision.
For this, the rock is first broken and grind into a powder of around one millimeter of grain size. Then the rock powder runs past a magnet that separates the tin forest from non-magnetic quartz. According to German Lithium, this process step could produce around 125,000 tonnes of tin forest concentrate per year. However, this deposition is always lost part of the tin forest and lands with the quartz rock in the room.
…then cleaning up to lithium carbonate
In order to obtain batter-based lithium salts, several chemical process steps must now follow. The German Lithium has already carried out pilot tests at a work in Weimar in 2018. For this purpose, the Erz concentrate is initially heated to around 1,00 degrees in a rotary oven. In this case, small beads are created, which are soluble in aqueous lyrics. This lithium-containing solution is then excluded by adding different acids in succession. In the end, lithium carbonate remains a white powder.
In testing with a similar procedure, the European Metals company reported an yield of 92 percent lithium in 2021. In each Locked Cycle test, lithium carbonate was used in battery quality, according to European Metals. This lithium carbonate could also be easily converted into lithium hydrooxide monohydrates with similar purity, a lithium salt also used for battery production.
If the production of lithium in the Erzgebirge is on a large scale, the tin-forest deposits could meet at least part of the German lithium needs. $8222; We assume that we will be in production in a larger framework in 2025, Müller said in autumn 2021. But whether this will really happen is still open.
Lithium extraction from the thermal water of the upper Rhine digging
White gold from geothermal
Germany not only has lithium-containing ore, but also in a dissolved form the „white gold is present: the deep waters of the upper Rhine digging form Europe's largest lithium resource. It is estimated that a total of 16 million tonnes of lithium equivalents could be solved there $211; and they could be significantly easier and more lucrative than lithium from solid ore.
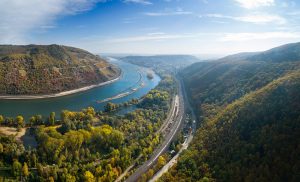
Enough lithium for one million batteries per year
The reason: along the upper Rhine grab there are already several geothermal plants that pump up the warm, salty low water for electricity and heat production. A year, up to two billion litres of thermal water flow through the lines. According to chemical analyses, the lithium part of these thermal waters is 160 to 190 milligrams per litre. $8222; If we consistently use this potential, we could meet a significant part of our needs in Germany, says geoscientist Jens Grimmer of the Karlsruher Institute for Technology (KIT).
It is estimated that the geothermal low water could be obtained from the low water of the upper Rhine's deep water per around 40,000 tonnes of lithium hydrogen water. That would be enough to meet the expected need for German battery production.
Direct extraction instead of evaporation
The technology necessary for this is already available. Unlike the classic lithium production from brine, electrochemical methods of direct lithium extraction (DLE) are used. 8222; They are faster than the classic evaporation metodes and avoid the use of chemicals, water consumption and the production of waste materials, explains Ernesto Calvo from the University of Buenos Aires. Instead, the lithium is separated from other salts by ion exchange, special adsorber materials and the use of electrodes and semble membrane.
At the upper Rhine, such procedures are already being tested in two pilot facilities, several other extraction facilities are under construction or planned. One of them is at the Geothermal power plant Insheim in Rheinland-Pfalz, which was recently taken over by Vulcan Energy. The aim of the company is to obtain lithium climate-neutral and sustainably from the geothermal water. However, the process must be adapted to the specific composition of deep water in the upper Rhine digging.
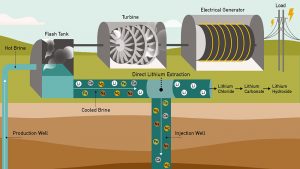
Insheim: Lithium without CO2 emissions
For the „Zero-Carbon lithium, the water in the pilot plant Insheim is initially guided by an extraction facility. There, undesirable elements such as sodium and potassium are captured by means of adsorber materials. A largely pure lithium chloride solution – according to Kreuter, the lithium amount reached a good 90 percent at first tests. In the next step, the lithium chloride will be converted into lithium hydrooxide by means of electrlysis. A first plant for this is to be created in the Frankfurt-Höchst chemistry park.
According to Kreuter, the lithium hydrooxide produced is supposed to be so pure that it can be used directly for the battery production of the automotive industry. The production costs are also significantly lower at a good 2,600 euros per tonne of lithium hydrooxide than in the classic extraction from brine or solid rock. As early as 2023, Vulcan wants to put into operation the first large-scale technology plant for lithium extraction at the Rhine digging, and from 2024, lithium hydrooxide is to be delivered to the car industry. There is already a new interest from the future customers: with Renault, Volkswagen, the Opel parent company and the battery manufacturer LG Chem, delivery contracts already exist.
Breakdown salt: Ion drive as lithium catcher
Other actors have also recognized the potential of lithium production in the course of geothermal. In Bruchsal, the power group EnBW will also install a pilot plant for lithium extraction together with the Karlsruhe Institute for Technology (KIT). There, the lithium is to be separated from the brine with an ion drive. This screen consists of manganganganxins that selectively bind lithium ions, while other salts flow through with the water unimpeded. The bound lithium is then chemically replaced from manganganoxide and converted into lithium hydrooxide.
Our break-saler plant works in a closed cycle. This means that neither gases nor liquids are delivered to the environment“, stresses Geothermal expert Thomas Kölbel of EnBW. The water transported from depth is pumped back into the ground after lithium extraction 䂿 as with normal geothermia systems.
The pilot plant wanted to show that it could also be able to implement sustainable and environmentally friendly production on an industrial scale. In the laboratory, the processes run with about 85- to 95 percent efficiency, and in real operation, an efficiency of about 70 percent. At around 8 000 hours of operation per year, the Bruchsal could then be given enough lithium for about 20,000 batteries alone. Because the lithium is quasi a by-product of geothermal, this is profitable, according to Kölbel and his team.