Hi Viv.
Your quite right re the inability to substitute some forms of stainless for particular apps.This is dependant on its physical characteristics as it relates to the environment in a chemical sense.
Now Im no exoert here having done only a couple of years chemistry at Uni.But what I do know is that they are different chemical interactions.
---------------------------------------------------
STAINLESS
In metallurgy, stainless steel is defined as an iron-carbon alloy with a minimum of 10.5% chromium content.[1] The name originates from the fact that stainless steel does not stain, corrode or rust as easily as ordinary steel. This material is also called corrosion resistant steel when it is not detailed exactly to its alloy type and grade, particularly in the aviation industry. As such, there are now different and easily accessible grades and surface finishes of stainless steel, to suit the environment to which the material will be subjected in its lifetime. Common uses of stainless steel are the everyday cutlery and watch straps.
Stainless steels have higher resistance to oxidation (rust) and corrosion in many natural and man made environments; however, it is important to select the correct type and grade of stainless steel for the particular application.
High oxidation resistance in air at ambient temperature is normally achieved with additions of a minimum of 13% (by weight) chromium, and up to 26% is used for harsh environments.[2] The chromium forms a passivation layer of chromium(III) oxide (Cr2O3) when exposed to oxygen. The layer is too thin to be visible, meaning the metal remains lustrous. It is, however, impervious to water and air, protecting the metal beneath. Also, this layer quickly reforms when the surface is scratched. This phenomenon is called passivation and is seen in other metals, such as aluminium and titanium. When stainless steel parts such as nuts and bolts are forced together, the oxide layer can be scraped off causing the parts to weld together. When disassembled, the welded material may be torn and pitted, an effect that is known as galling.
Nickel also contributes to passivation, as do other less commonly used ingredients such as molybdenum and vanadium.
GALVANISED
Zinc Coatings
Zinc coatings prevent corrosion of the protected metal by forming a barrier, and by acting as a sacrificial anode if this barrier is damaged. When exposed to the atmosphere, zinc reacts with oxygen to form zinc oxide, which further reacts with water molecules in the air to form zinc hydroxide. Finally zinc hydroxide reacts with carbon dioxide in the atmosphere to yield a thin, impermeable, tenacious and quite insoluble dull gray layer of zinc carbonate which adheres extremely well to the underlying zinc, so protecting it from further corrosion, in a way similar to the protection afforded to aluminum and stainless steels by their oxide layers.
Hot dip galvanizing deposits a thick, robust layer that may be more than is necessary for the protection of the underlying metal in some applications. This is the case in automobile bodies, where additional rust proofing paint will be applied. Here, a thinner form of galvanizing is applied by electroplating, called "electrogalvanization". However, the protection this process provides is insufficient for products that will be constantly exposed to corrosive materials such as salt water. Nevertheless, most nails made today are electro-galvanized.
Galvanic protection (also known as sacrificial-anode or cathodic protection) can be achieved by connecting zinc both electronically (often by direct bonding to the protected metal) and ionically (by submerging both into the same body of electrolyte, such as a drop of rain). In such a configuration the zinc is absorbed into the electrolyte in preference to the metal that it protects, and maintains that metal's structure by inducing an electric current. In the usual example, ingots of zinc are used to protect a boat's hull and propellers, with the ocean as the common electrolyte.
As noted previously, both mechanisms are often at work in practical applications. For example, the traditional measure of a coating's effectiveness is resistance to a salt spray. Thin coatings cannot remain intact indefinitely when subject to surface abrasion, and the galvanic protection offered by zinc can be sharply contrasted to more noble metals. As an example, a scratched or incomplete coating of chromium actually exacerbates corrosion of the underlying steel, since it is less electrochemically active than the substrate.
Galvanized surface with visible spangleThe size of crystallites in galvanized coatings is an aesthetic feature, known as spangle. By varying the number of particles added for heterogeneous nucleation and the rate of cooling in a hot-dip process, the spangle can be adjusted from an apparently uniform surface (crystallites too small to see with the naked eye) to grains several centimeters wide. Visible crystallites are rare in other engineering materials. Protective coatings for steel constitute the largest use of zinc and rely upon the galvanic or sacrificial property of zinc relative to steel.
----------------------------------------------------
In apps where sterility and cleanliness is required high grade stainless is the only option.
In the construction/infrastructure industry higher grades of gal are definitely an option and these are volume apps whereas those sterility/cleanliness apps arnt,which MAY suport your thought that there could be a quantum move to gal and hence higher zinc usage given the price of nickel atm.
However one should temper this thinking in that the nickel stockpile has made a SLIGHT move up which MIGHT intimate such substitution occurring.BUT this current nickel stockpile move is hardly STRONGLY indicative of such a move as the stockpile is still at a very critical level.
I really cant comment on the dynamics of the nickel stockpile as I havnt been watching it very closely so Im not sure if this slight build is due to inflow or a lack of demand which would give rise to the hypothesis that substitution was occuring if demand had dropped.The complicating issue here is the high nickel price which would motivate some to take profits on their nickel holdings,be they funds or physical.
Theres no doubt that zinc is a much cheaper alternative to stainless and when combined with the volume use in the infrastructure/construction fields we could see,or even be seeing,much stronger demand for zinc due to its much sheaper base cost.As
As my posts have indicated there is strong information now to imply that China is using much more zinc than we first thought.The MI data doesnt line up with the Antaike data and as the MI reports suggest there is still not the artisan industry being accounted for in terms of smelting and consumtion.
The thing that backs this thinking STRONGLY is the "UNHIDEABLE" Chinese demand for high grade iron ore.Zind demand follows this like a puppy dog.
Add to this the huge increase in the Chinese smletinmg capacity for zinc and the black hole that China is becoming for zinc concentrate and imo we have a strengtheneing scenario for zinc.
This is backed by the likes of Ian Henderson(senior JPM analysts thoughts which I recently posted)and Dr Shane Oliver of AMP who has been very much on the mark with his insights into the developing world economies.
d.
- Forums
- ASX - By Stock
- AIM
- what a difference a day ecn
AIM
ai-media technologies limited
Add to My Watchlist
0.00%
!
53.0¢
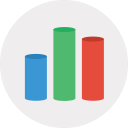
what a difference a day ecn, page-25
Featured News
Add to My Watchlist
What is My Watchlist?
A personalised tool to help users track selected stocks. Delivering real-time notifications on price updates, announcements, and performance stats on each to help make informed investment decisions.
|
|||||
Last
53.0¢ |
Change
0.000(0.00%) |
Mkt cap ! $110.6M |
Open | High | Low | Value | Volume |
53.0¢ | 53.0¢ | 50.5¢ | $160.7K | 308.2K |
Buyers (Bids)
No. | Vol. | Price($) |
---|---|---|
3 | 12100 | 52.0¢ |
Sellers (Offers)
Price($) | Vol. | No. |
---|---|---|
53.0¢ | 4761 | 1 |
View Market Depth
No. | Vol. | Price($) |
---|---|---|
2 | 11100 | 0.520 |
1 | 15000 | 0.510 |
4 | 23796 | 0.500 |
1 | 10000 | 0.495 |
1 | 2000 | 0.490 |
Price($) | Vol. | No. |
---|---|---|
0.540 | 9500 | 1 |
0.570 | 10000 | 1 |
0.590 | 1973 | 1 |
0.620 | 250 | 1 |
0.645 | 7163 | 2 |
Last trade - 16.10pm 11/07/2025 (20 minute delay) ? |
Featured News
AIM (ASX) Chart |
The Watchlist
VMM
VIRIDIS MINING AND MINERALS LIMITED
Rafael Moreno, CEO
Rafael Moreno
CEO
SPONSORED BY The Market Online